Łączenie poszczególnych modułów maszyn w ciągłą linię może być bardzo pracochłonne i zajmuje dużo miejsca. Firmie Optima udało się połączyć maszynę napełniającą i pakującą, tworząc jeden płynny proces. Stało się to możliwe dzięki unikalnemu rozwiązaniu wykorzystującemu inteligentny system transportowy ACOPOStrak firmy B&R.
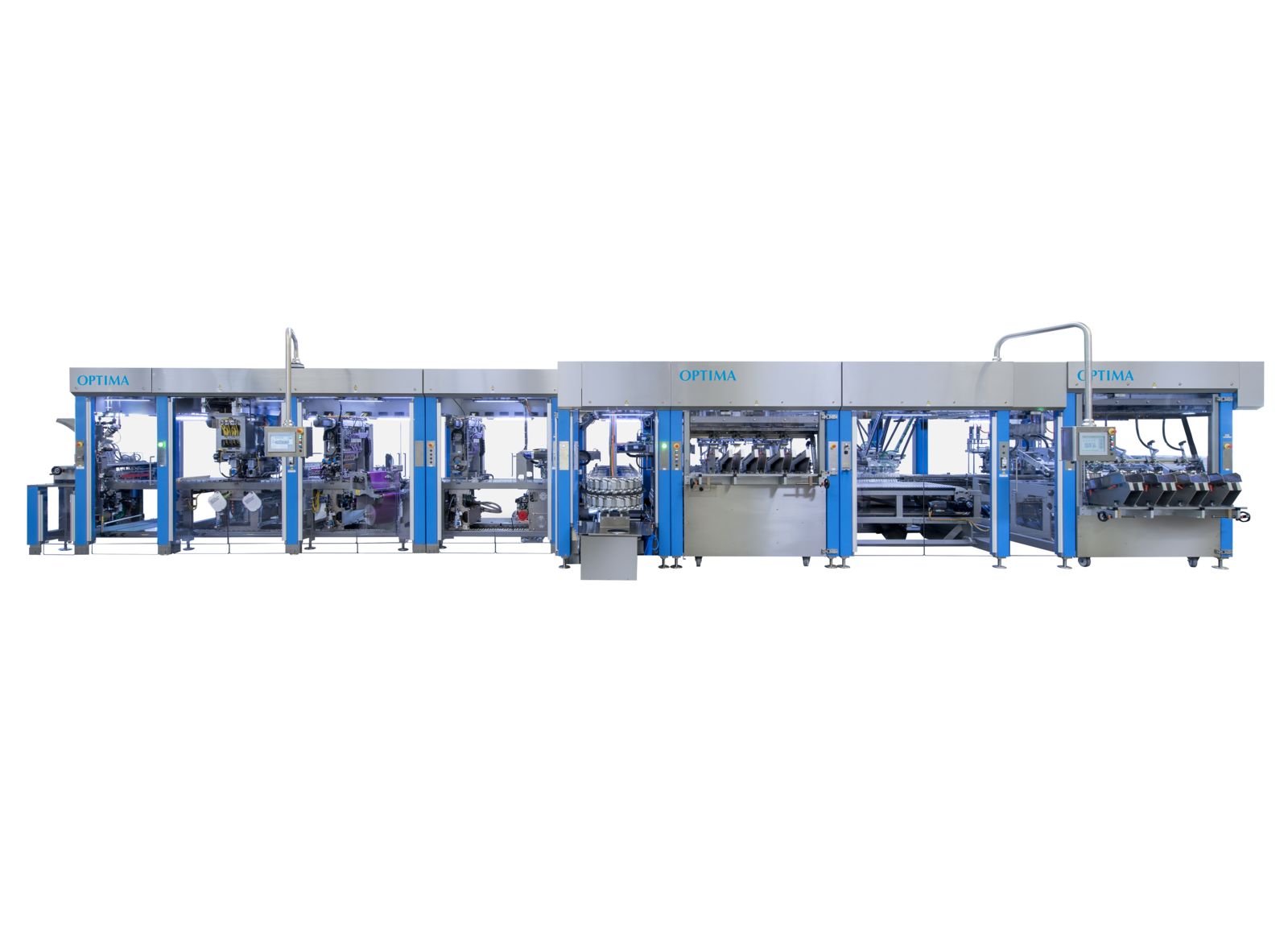
„Dla nas, konstruktorów maszyn, łączenie różnych modułów maszyn jest zawsze szczególnym wyzwaniem” – mówi Andreas Dreschner, technical sales manager w firmie Optima. Kiedy wiosną 2019 roku Optima rozpoczęła realizację projektu, oceniono możliwe systemy transportowe łączące urządzenia do napełniania i pakowania. „W przypadku naszej aplikacji nie było innego systemu, który oferowałby taką elastyczności i spełniał nasze wymagania dotyczące prędkości i dynamiki w takim samym stopniu, co ACOPOStrak” – wyjaśnia Dreschner.
Nowa aplikacja została po raz pierwszy zastosowana w linii napełniającej i pakującej w holenderskiej firmie spożywczej do produkcji pojedynczych aluminiowych kapsułek kawy. Każdy wózek został wyposażony w nośnik produktu mieszczący jedną kapsułkę kawy, co oznacza, że każda kapsułka może być przemieszczana przez linię całkowicie niezależnie od pozostałych. Umożliwia to grupowanie dowolnej liczby kapsułek na bieżąco podczas transportu.
Płynny przebieg produkcji
„Jednym z problemów w przypadku tej aplikacji były luki powstające podczas procesu produkcyjnego” – wspomina Dreschner. Dzieje się tak na przykład wtedy, gdy kapsułki są odrzucane, gdyż nie przeszły kontroli jakości. Nawet niewielkie odchylenie w wadze, niedoskonałe uszczelnienie lub niewielkie przesunięcie w położeniu wieczka może spowodować odrzucenie kapsułki, dlatego operatorzy instalacji przyjmują wskaźnik odrzutów na poziomie około 0,2 do 0,3 procent. „Kapsułki są zazwyczaj pakowane w kartony po dziesięć lub więcej sztuk, co w konsekwencji prowadzi do jeszcze większego odsetka wadliwych kartonów.”
Zdolność wózków ACOPOStrak do niezależnego poruszania się umożliwia łatwe likwidowanie wszelkich luk w przepływie produkcji. Kapsułki, które nie przejdą kontroli jakości, są od razu usuwane. „ACOPOStrak natychmiast przesuwa na ich miejsce następne kapsułki, a przepływ produktów jest kontynuowany bez utraty rytmu” – wyjaśnia Dreschner.
Elastyczne grupowanie
Po napełnieniu i zamknięciu kapsułek z kawą, linia napełniająca przekazuje po dwanaście kapsułek do następnego etapu produkcji. Wejście linii pakującej ma natomiast piętnaście torów. Również na tej linii doskonale sprawdzają się elastyczne wózki systemu transportowego B&R. ACOPOStrak odbiera grupy po dwanaście kapsułek z maszyny napełniającej, a zanim dotrą one do wejścia pakującego, są już przegrupowywane w zestawy po piętnaście sztuk.
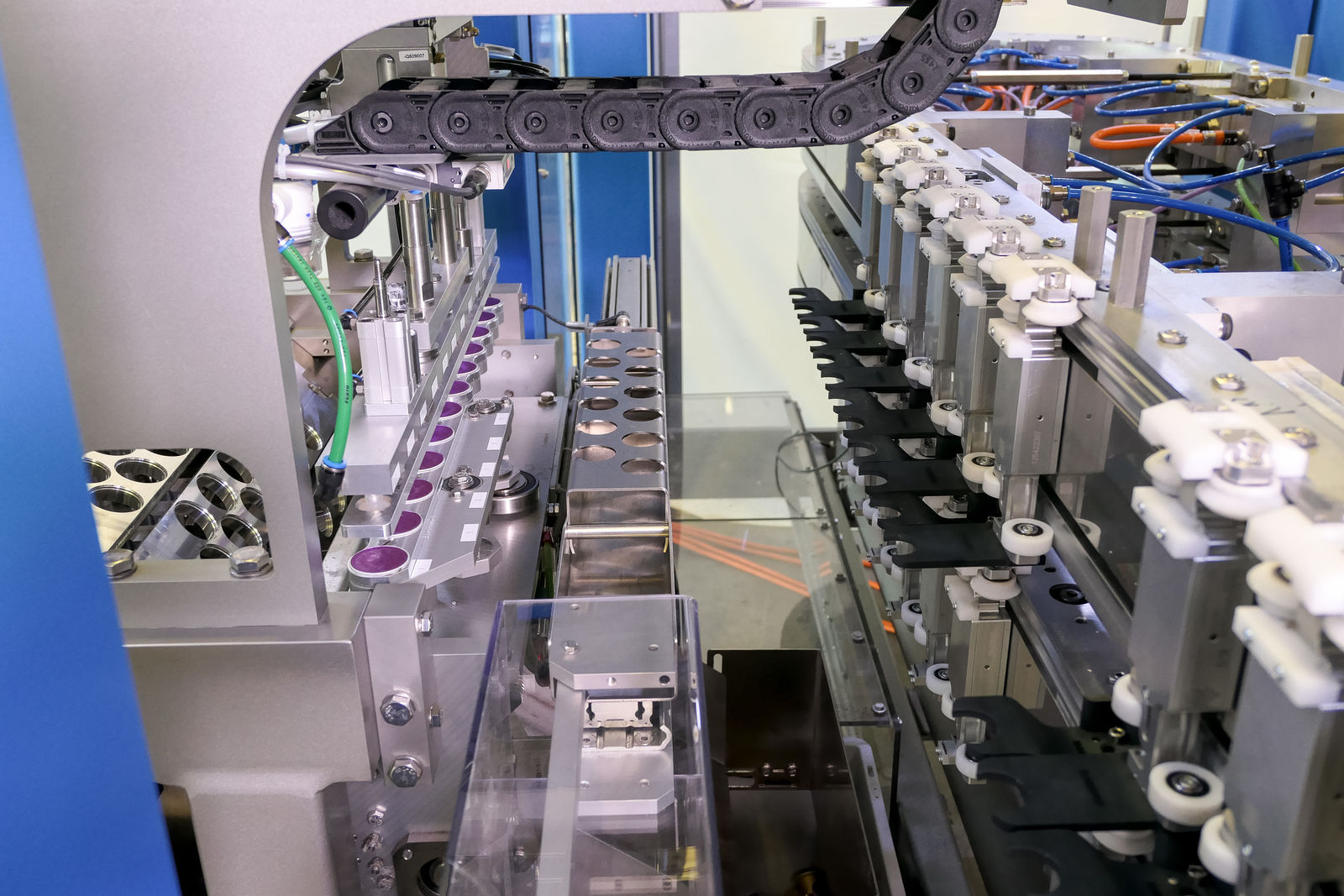
Konfigurowanie zestawów na bieżąco
Różne zestawy produktów, które mają być pakowane razem, są zwykle układane za pomocą ślimaków podających, kół podających, pasów i łańcuchów. Aby maszyna mogła wyprodukować inną konfigurację zestawu, sprzęt musi zostać zmodyfikowany ręcznie. W przypadku systemu Optima wózki zdecydowanie ułatwiają przezbrojenie pomiędzy zestawami. Konfiguracje można zmieniać na bieżąco podczas pracy, wybierając po prostu odpowiednią recepturę na terminalu operatora.
Zaoszczędzone cztery metry
Pod względem powierzchni, innowacyjne rozwiązanie zastosowane w Optimie ma wyraźną przewagę nad systemami wykorzystującymi konwencjonalną technologię grupowania produktów. „W przypadku konwencjonalnej konstrukcji z użyciem ślimaków, funkcja grupowania wymaga zastosowania ramy maszyny z dwoma polami, każde o długości 220 centymetrów” – wyjaśnia Dreschner. „Nowe rozwiązanie ACOPOStrak zwiększa jednak całkowitą długość systemu jedynie o 80 centymetrów, dzięki czemu jest on prawie cztery metry krótszy niż poprzednio.”
Mimo to osiąga wyższą przepustowość niż jego konwencjonalny odpowiednik: holenderska firma spożywcza produkuje i pakuje 720 kapsułek w 72 kartony na minutę. Łącznie w obiegu znajduje się 80 wózków. Są one rozmieszczone na dwóch oddzielnych, spiętrzonych owalnych torach, każdy o długości 7,2 metra. Przyspieszenie wózków wynosi 30 m/s² a ich maksymalna prędkość to 2,6 m/s.
Jednym z powodów podziału na dwa tory były wymagane odstępy między produktami poniżej 50 mm, chociaż same wózki mają już 50 mm szerokości. Dlatego też owale toru i nośniki produktów są skonstruowane w taki sposób, że chwytaki górnego i dolnego owalu zatrzymują się na przemian na tym samym poziomie. Na tym poziomie nośniki produktów mają szerokość tylko około 40 mm, dzięki czemu można osiągnąć wymaganą odległość między produktami poniżej 50 mm.
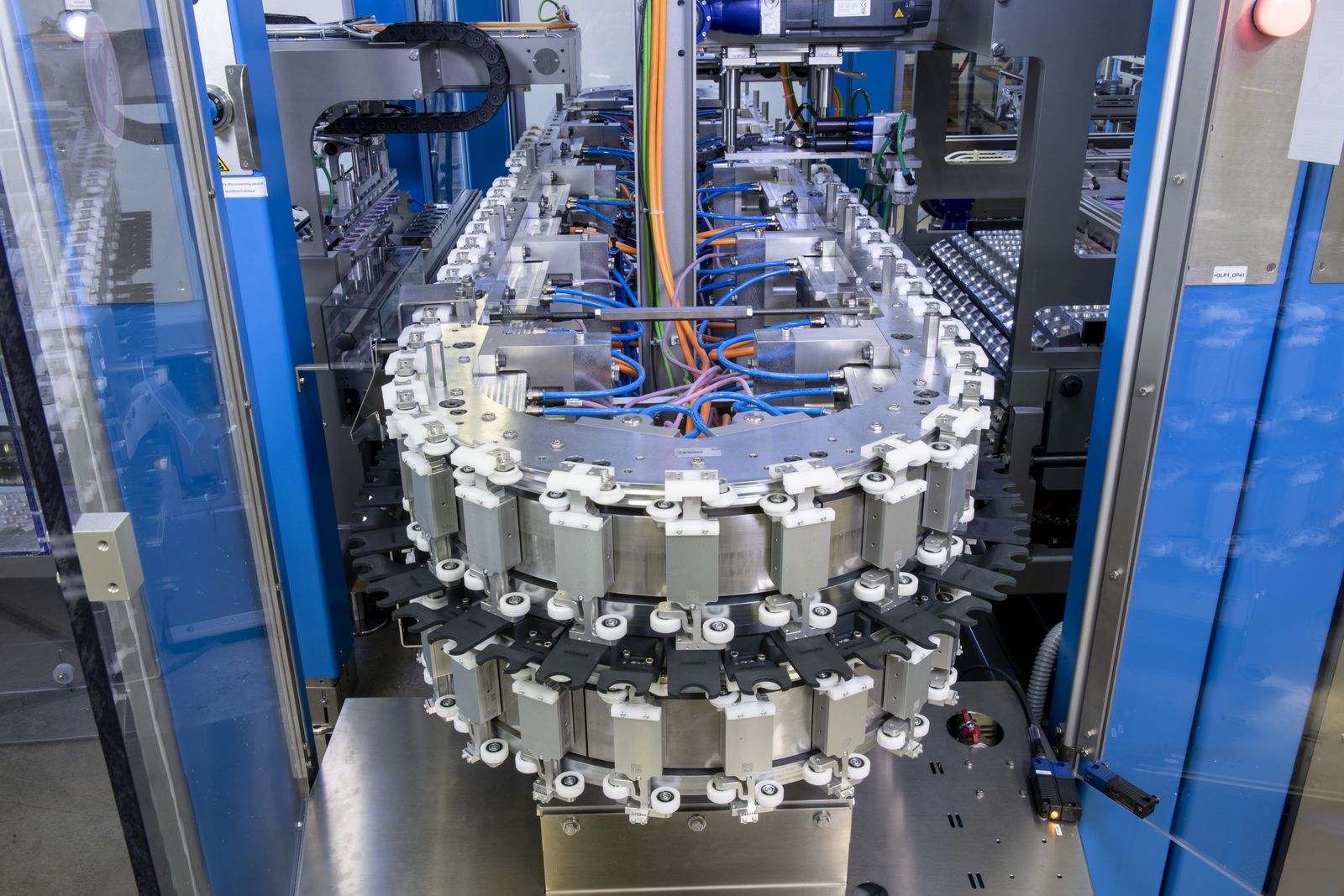
Precyzyjny transport
Pomimo dynamicznych osiągów, przemieszczanie kapsułek odbywa się w sposób niezwykle ostrożny. „W porównaniu z konwencjonalnym procesem grupowania znacznie zredukowaliśmy liczbę etapów produkcji” – twierdzi Dreschner. „Nośniki produktu zapobiegają również obijaniu się kapsułek o siebie podczas przegrupowywania.” Dlatego ACOPOStrak szczególnie nadaje się do produktów wrażliwych, takich jak wysokiej klasy aluminiowe kapsułki jednokrotnego użytku na kawę.
Symulacja usprawnia projektowanie
Inteligentne opcje symulacji oferowane przez oprogramowanie inżynierskie B&R były bardzo pomocne przy opracowywaniu maszyny. Dreschner: „Dzięki możliwości przeprowadzania symulacji w oparciu o naszą wstępną koncepcję wcześnie zdaliśmy sobie sprawę, że jeden tor nie wystarczy.
Po wprowadzeniu dwóch torów i powtórzeniu symulacji, mogliśmy ruszyć z miejsca, mając pewność, że proces transportu będzie przebiegał zgodnie z planem i że uzyskamy wymagane przez klienta parametry wydajnościowe bez żadnych nieprzyjemnych niespodzianek na późniejszych etapach projektu.” Dodatkowy nakład pracy związany z symulacją był minimalny. Optima była w stanie przyswoić wszystkie reguły procesowe opracowane na potrzeby symulacji i zastosować je w rzeczywistej aplikacji maszyny za naciśnięciem jednego przycisku.
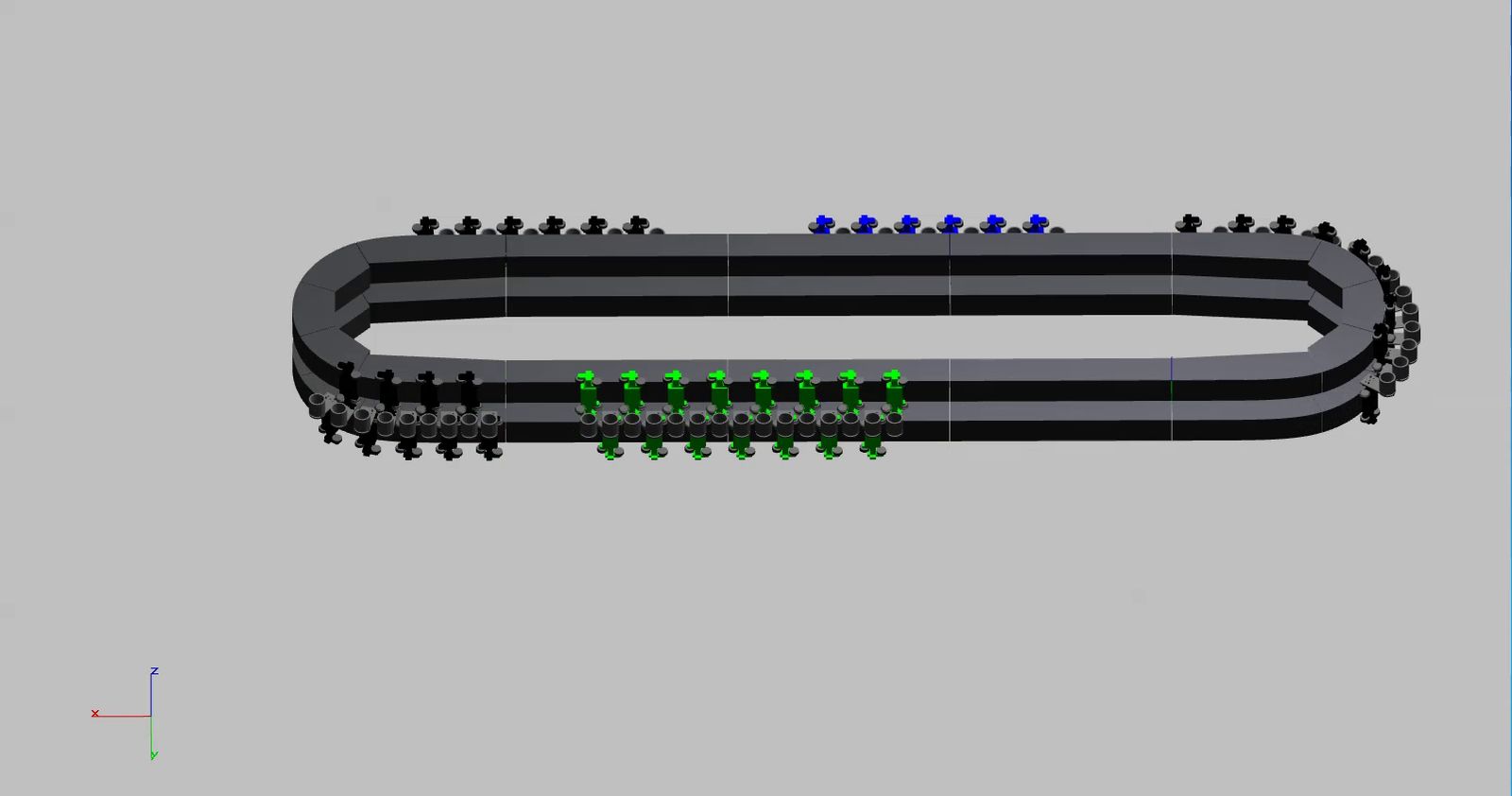
Innowacyjna technologia zapewnia przewagę konkurencyjną
Modułowa konstrukcja, niekomplikowany proces programowania ruchu wózków i wsparcie ekspertów B&R pomogły przyspieszyć proces uczenia się nowej technologii w firmie Optima. „Na początku pierwszego projektu ACOPOStrak był jeszcze częściowo w stadium prototypu” – zauważa Dreschner. „Współpraca między wszystkimi stronami zaangażowanymi w projekt układała się bardzo dobrze. Pracowników wszystkich szczebli – od programistów aż po najwyższe kierownictwo – jednoczył ten sam cel. To właśnie pozwoliło nam w krótkim czasie przygotować system do użytku przemysłowego.” Wysiłki się opłaciły: pierwszy dostarczony system już działa bez problemów, w trybie ciągłym, ku zadowoleniu wszystkich zainteresowanych.
I jeszcze jedno: „Rozwiązanie to wyznacza nowy etap w naszym rozwoju i naprawdę robi piorunujące wrażenie na każdym, kto widzi je w działaniu” – zapewnia Dreschner. „Nikt inny nie oferuje podobnego systemu na naszym rynku. Dotyczy to szczególnie producentów marek własnych, którzy muszą produkować dla wielu różnych klientów i zawsze szukali możliwości takiego elastycznego, bieżącego grupowania produktów, które my możemy teraz zaoferować.”
- Zalety grupowania z użyciem ACOPOStrak
- Oszczędność powierzchni
- Elastyczne grupowanie
- Wyeliminowanie przerw w przepływie produktów
- Wysoka wydajność
- Precyzyjny transport produktów
- Konstrukcja dla klasy spożywczej
![]() | Andreas Dreschner Technical Sales Manager, Optima „W przypadku naszej aplikacji nie było innego systemu, który oferowałby taką elastyczność i spełniał nasze wymagania dotyczące prędkości i dynamiki w takim samym stopniu, co ACOPOStrak.” |