Los sistemas de transporte inteligentes con lanzaderas controladas de manera independiente allanan el camino para la producción a gran escala de lotes de una unidad. No obstante, la única forma de que esto funcione de verdad es si se pueden reducir drásticamente los gastos generales de desarrollo para programar los movimientos de la lanzadera, utilizando un software de sistema inteligente como mapp Trak de B&R.
Los productos con un toque personal no son solo un reclamo: despiertan en los consumidores un intenso deseo de comprarlos. Cada vez más fabricantes buscan asegurar su cuota de beneficios en la personalización a gran escala equipando sus plantas con sistemas de transporte inteligentes basados en pistas. No obstante, la personalización a gran escala solo es rentable si el sistema de pistas es lo bastante flexible como para aceptar variantes de productos o productos completamente nuevos de una forma rápida y económica.
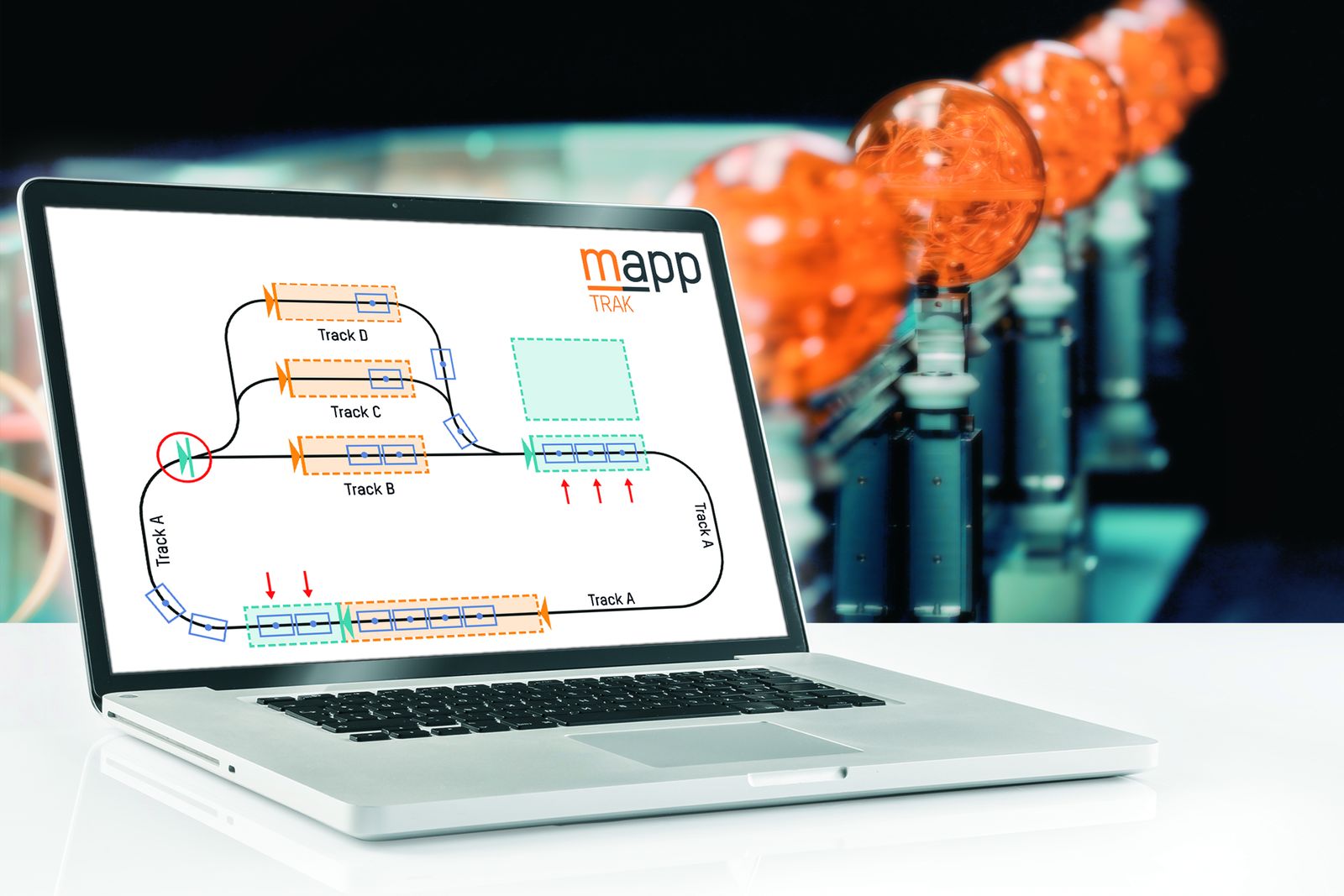
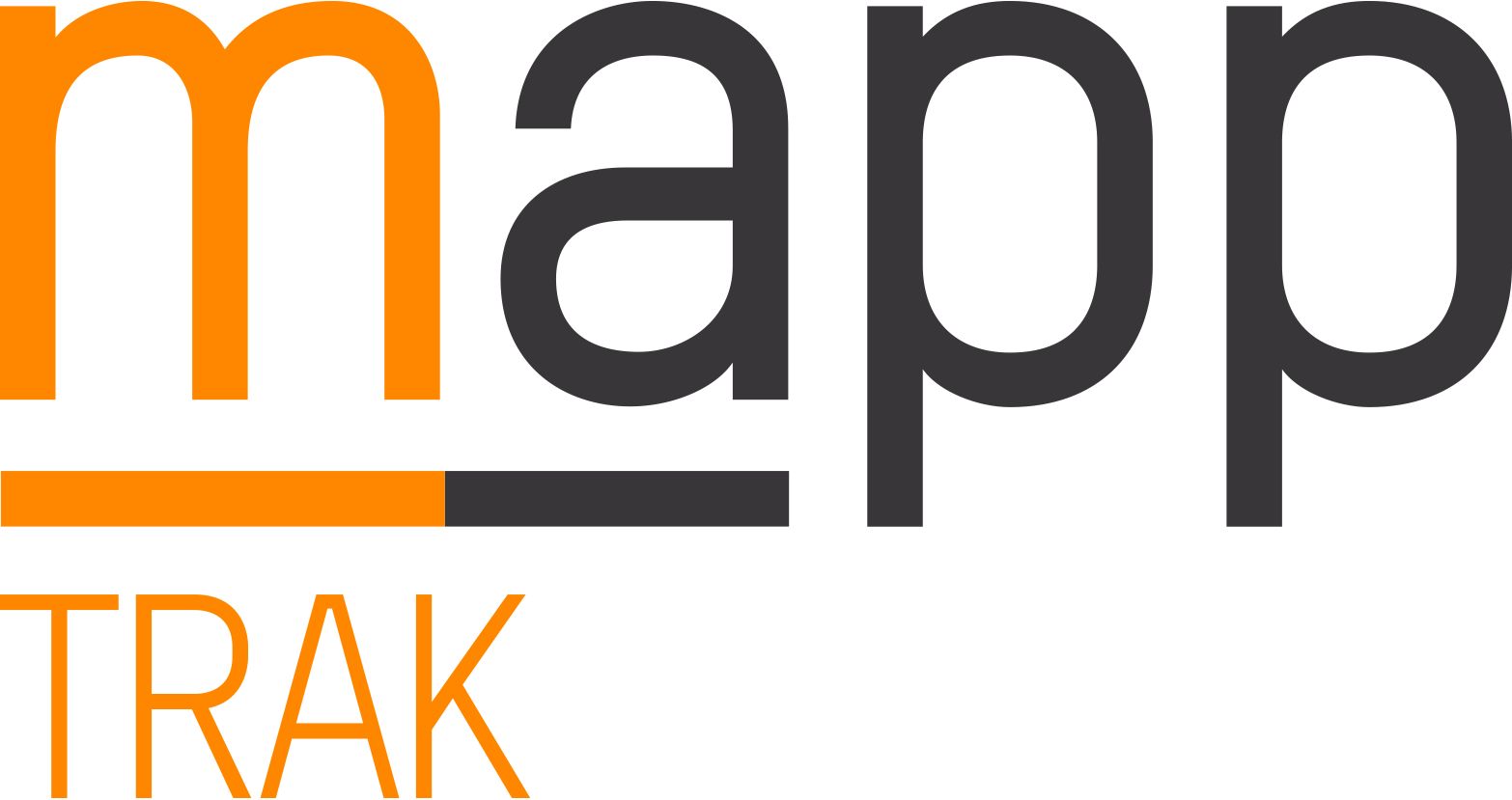
Y eso es exactamente lo que hace el sistema de transporte inteligente ACOPOStrak de B&R. El sistema tiene una estructura modular, con cuatro elementos de pista básicos y desviadores que le permiten transformarse en prácticamente cualquier diseño y adaptarse o ampliarse fácilmente en cualquier momento. Las lanzaderas de accionamiento electromagnético pueden controlarse de manera independiente, aunque estén situadas en un lateral del desviador.
La arquitectura del sistema es muy adaptable y permite diseños con pistas de una longitud superior a 100 metros que incluyen cientos de lanzaderas. Y además: «A pesar de la complejidad del sistema de pistas, es fácil de manejar», explica Robert Kickinger, director de tecnologías mecatrónicas de B&R. B&R ha
simplificado el proceso de diseño de las soluciones ACOPOStrak para ayudar tanto a los fabricantes de máquinas como a las empresas de fabricación a comercializar sus productos de la forma más rápida posible. «Si se minimiza el trabajo de ingeniería y los costes asociados, también se puede conseguir un interesante retorno de la inversión», añade Kickinger.
Colisión imposible
Para conseguirlo, lo que necesitan el fabricante de equipos originales o el operario de la máquina es el software de sistema mapp Trak que se entrega con el sistema ACOPOStrak. «Este software es el resultado del trabajo de nuestros ideólogos en desarrollo», explica el especialista en mecatrónica. Han dominado las complejas tareas matemáticas que subyacen en las principales funciones de ACOPOStrak,
incluyendo la prevención de colisiones, dividiendo y fusionando flujos de productos a toda velocidad y calculando las rutas óptimas. Al no tener que preocuparse por estas tareas, los desarrolladores de aplicaciones se ahorran un valioso tiempo de ingeniería.
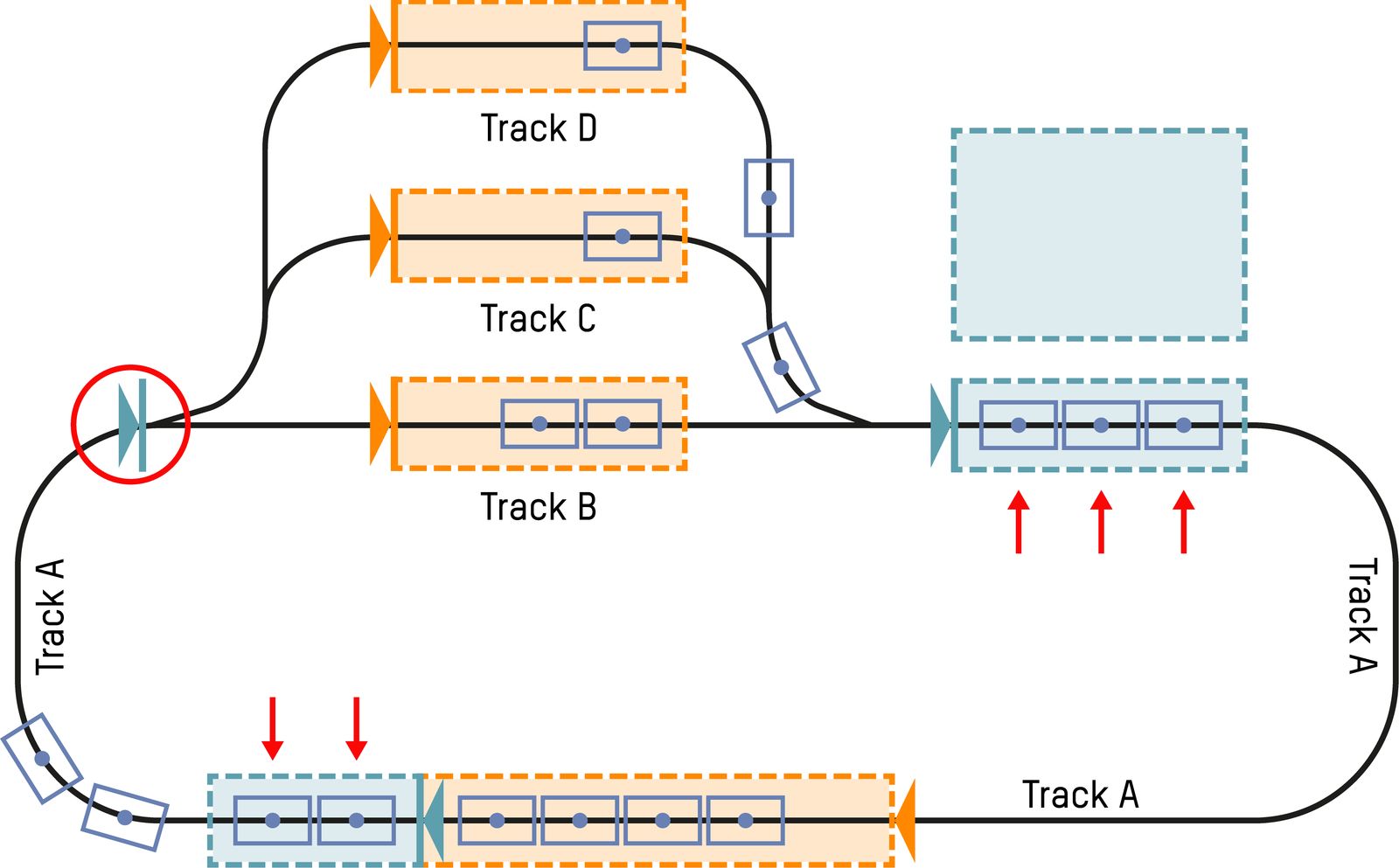
Incluso con productos de diferentes tamaños y pesos, no se producen colisiones. El tamaño del producto puede configurarse manualmente o medirse con sensores, y mapp Trak ajusta automáticamente los controles de la lanzadera para evitar colisiones.
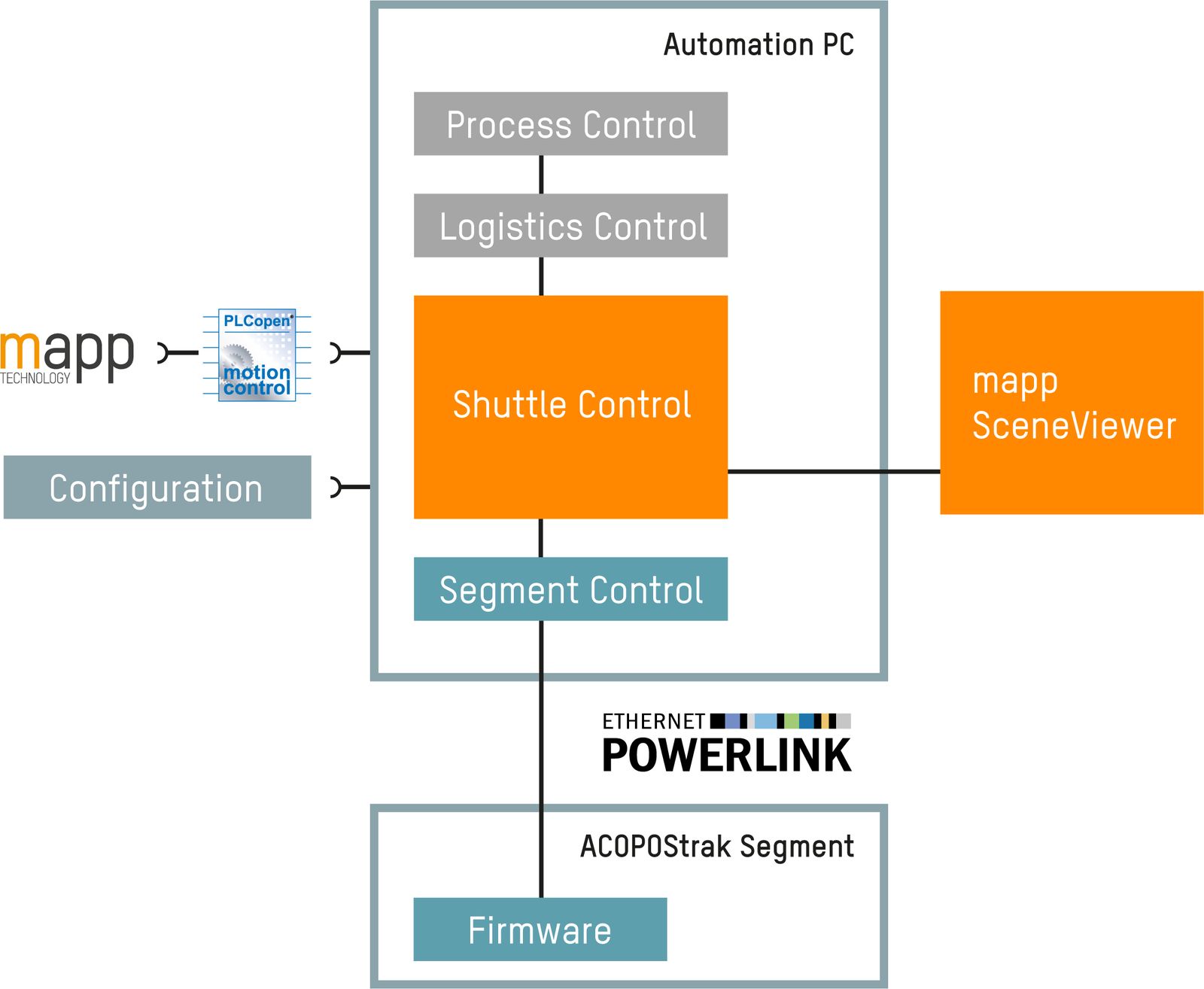
Programación orientada en función de los procesos
Un segundo factor que simplifica notablemente el proceso de ingeniería es la programación orientada en función de los procesos. Con mapp Trak, el ingeniero de software define las reglas acerca de cómo deben comportarse las lanzaderas en la pista. Las reglas se activan cuando las lanzaderas pasan por puntos de activación virtuales. Esta sencilla metodología basada
en las máquinas de estado hace que la implementación de secuencias de movimiento sea extremadamente eficiente.
Con ACOPOStrak, no es necesario programar ejes y perfiles de movimiento para cada lanzadera de forma individual, una tarea excesivamente laboriosa si tenemos cientos de lanzaderas y
muchos posibles rutas. Otra de las ventajas de la programación orientada en función de los procesos
es que las lanzaderas pueden retirarse de o añadirse a la pista sin que deba realizarse ningún cambio en el software de la aplicación.
Simulación para un funcionamiento eficiente
Las funcionalidades de simulación integradas en mapp Trak ofrecen una clara confirmación visual de que el sistema funcionará sin problemas. Los desarrolladores pueden probar con cuántas lanzaderas y a qué velocidad la aplicación conseguirá la máxima productividad. «Pueden simular varios supuestos en el ordenador de su oficina sin las limitaciones ni los riesgos que comporta un sistema real», comenta Davide Migliorisi, gerente de proyectos de B&R para sistemas de pistas. Este software es idéntico al software del sistema que posteriormente se utilizará en el control. Puede alternarse en cualquier momento entre el funcionamiento simulado y el real.
También puede utilizarse Scene Viewer para visualizar cómo interactúan las lanzaderas con elementos mecánicos adicionales, como por ejemplo destornilladores, etiquetadoras o robots. Todo lo que debe hacerse es importar un archivo STEP del elemento de máquina respectivo y modelar su movimiento en el espacio a lo largo del tiempo. Esto permite al desarrollador no solo simular la pista, sino también la interacción con los elementos adicionales de la máquina. «Nuestros clientes aprecian mucho este sentido práctico de la capacidad de simulación de mapp Trak», confirma Migliorisi.
«Y la interacción con elementos mecánicos externos funciona tan bien», añade, «porque ACOPOStrak incorpora los genes de la familia de servoaccionamientos ACOPOS». La familia ACOPOS dispone de sofisticadas funciones para operar sistemas de uno o varios ejes, así como de multitud de opciones para el acoplamiento entre ejes.
Por lo tanto, las lanzaderas pueden coordinarse estrechamente con los ejes impulsados por los servoaccionamientos ACOPOS utilizando comandos PLCopen, y mostrarse como gemelos digitales en Scene Viewer.
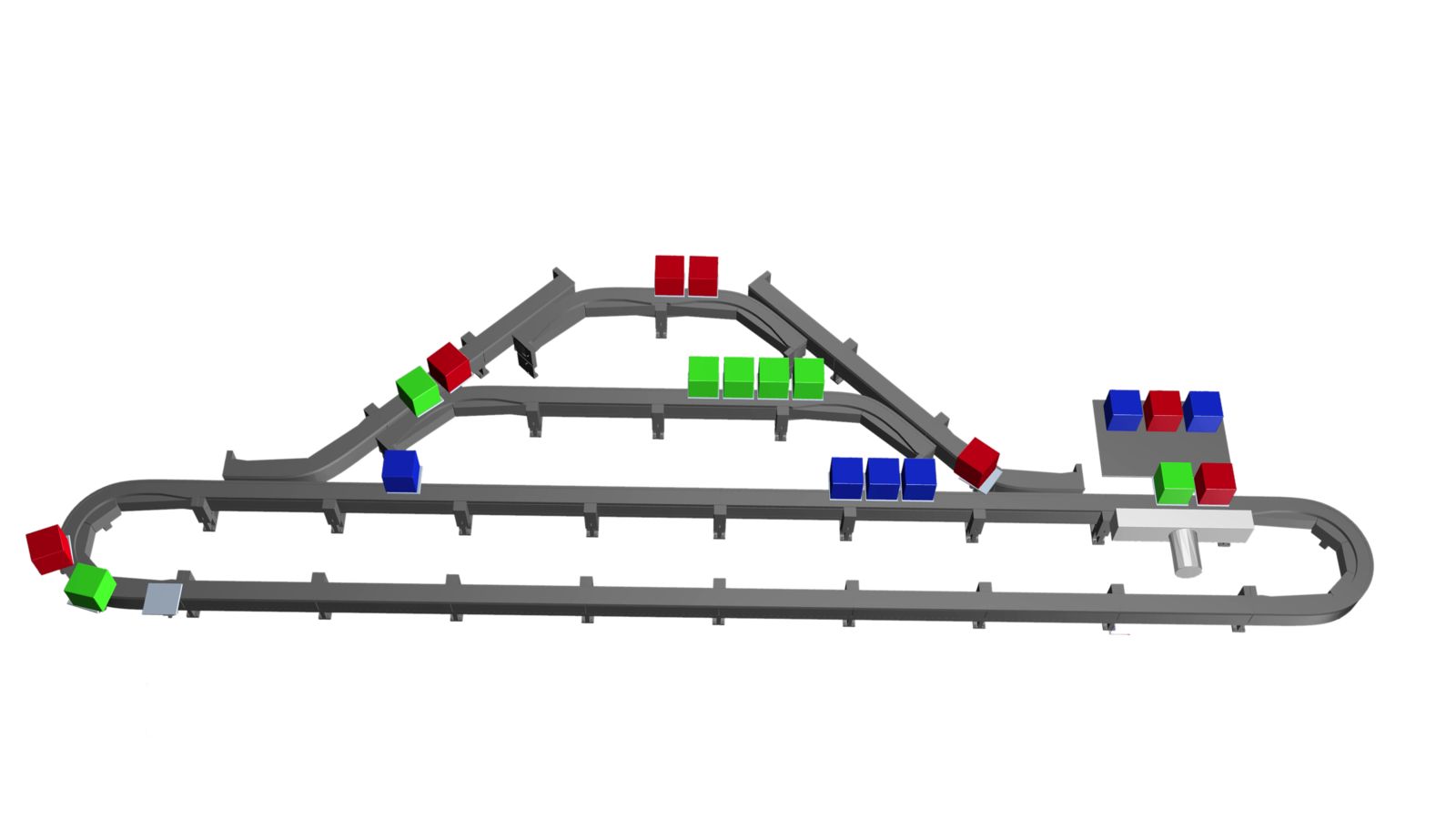
Máxima flexibilidad
Los clientes ya han confirmado que ACOPOStrak es fácil de manejar. Kickinger informa que un cliente que había ampliado una máquina con segmentos de motor lineal adicionales utilizando ACOPOStrak solo tuvo que dedicar quince minutos al desarrollo del software antes de que la máquina volviera a estar en funcionamiento. Esta es una impresionante muestra de la capacidad del concepto de programación de ACOPOStrak, que está desacoplado del hardware.
Con el software del sistema mapp Trak, los datos del producto pueden vincularse claramente a la lanzadera en la que se encuentra actualmente el respectivo producto. «Esto te ofrece el máximo grado de flexibilidad», explica Kickinger. Un registro de datos específicos del producto en una línea de producción farmacéutica, por ejemplo, puede contener la composición exacta del
ingrediente activo y un identificador exclusivo. También puede almacenarse la fecha y la hora en que cada producto pasa a través de cada estación de procesamiento. Esto facilita que los ingenieros de sistemas implementen el seguimiento compatible con la FDA.
Complejidad manejable
mapp Trak garantiza tres cosas: que las lanzaderas no colisionan, que no cruzan barreras virtuales y que se respetan los límites de velocidad configurables. Con estas garantías, la sencilla programación y la simulación integrada, B&R ha hecho que el sistema de transporte flexible ACOPOStrak sea muy fácil de manejar para el usuario. Esto también permite implementar nuevos productos en lotes de cualquier tamaño, de forma rápida y con unos gastos generales mínimos. Este es un aspecto crucial para conseguir nuevos pedidos de producción a corto plazo.
Autor: Carmen Klingler-Deiseroth, periodista independiente
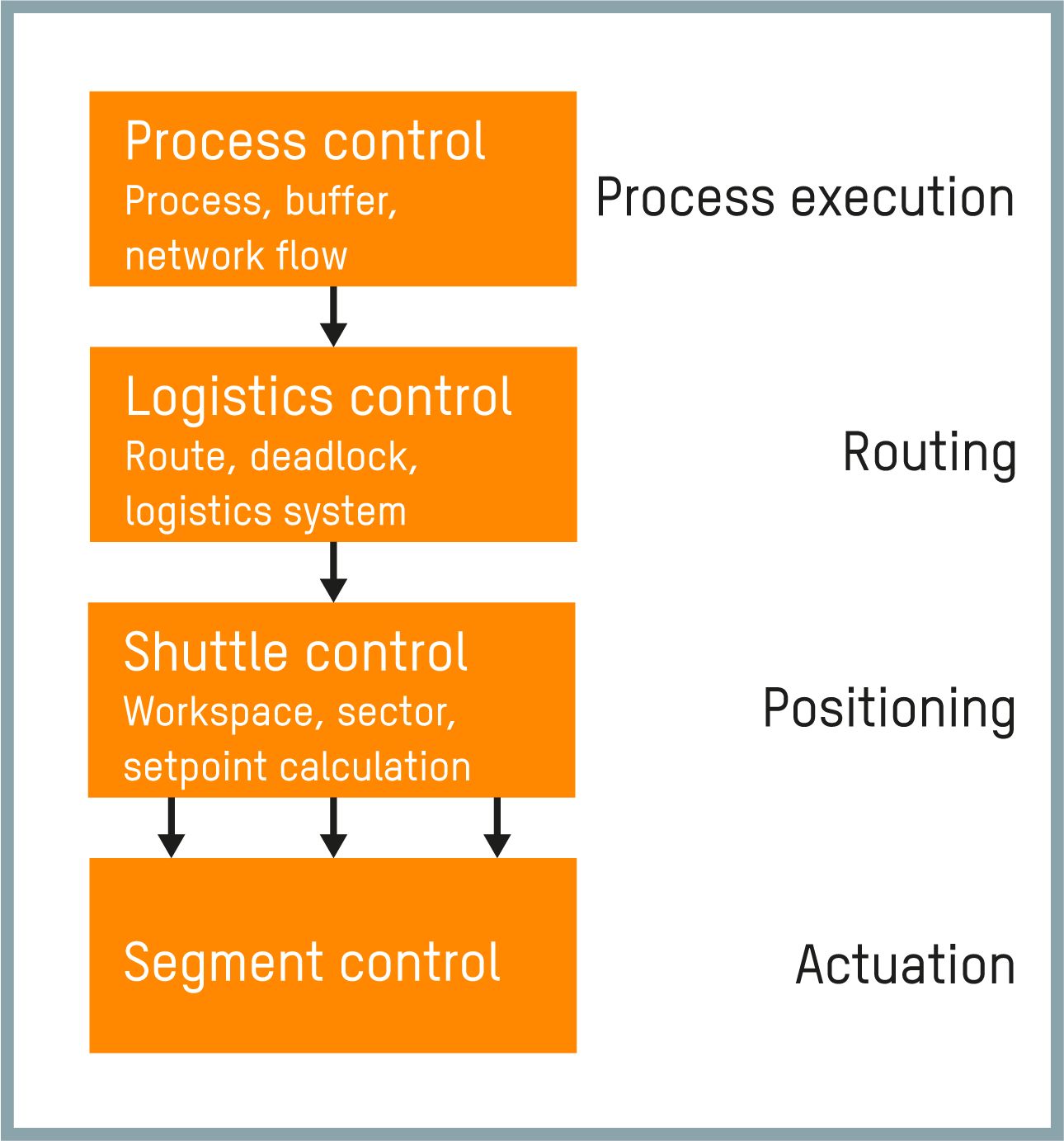
La arquitectura de mapp Trak
La arquitectura de software de mapp Trak se divide en cuatro niveles básicos. El más bajo, el nivel de control de segmento, controla el movimiento de las lanzaderas ubicadas en el segmento respectivo.
La siguiente capa superior, el nivel de control de la lanzadera, es donde se calculan aspectos como los puntos de ajuste de posición para las lanzaderas. Si el ingeniero de sistemas desea acoplar las lanzaderas a un eje externo o a otra lanzadera, por ejemplo utilizando bloques de funciones PLC, se produce en este nivel. Este es también el nivel en el que se manejan las lanzaderas que se añaden y se retiran de la pista, por ejemplo cuando se utiliza ACOPOStrak en combinación con cintas transportadoras convencionales, o si los operarios o los robots añaden y retiran lanzaderas.
Los elementos de software del tercer nivel, el control de la logística, proporcionan un enrutamiento automatizado desde una estación de procesamiento a otra.
El cuarto nivel está dedicado al control de procesos. Este nivel también representa la interfaz de programación para que el ingeniero de software describa el flujo del proceso.