Les systèmes de transport intelligents avec navettes contrôlées individuellement jettent les bases de la customisation de masse. Ce nouveau paradigme de production ne peut se réaliser que si l'effort de programmation à consentir pour ces systèmes de transport est limité. Le logiciel mapp Trak de B&R a été conçu pour répondre à ce besoin d'efficacité.
Un produit personnalisé ne fait pas qu'attirer le regard du consommateur visé. Il éveille aussi en lui le désir de le posséder. Aussi, de plus en plus de fabricants cherchent à personnaliser leur production en s'équipant de systèmes de transport intelligents à pistes électromagnétiques. Néanmoins, cette démarche ne peut porter ses fruits que si le système de transport est suffisamment flexible pour passer rapidement d'un produit à l'autre sans que cela génère des coûts importants.
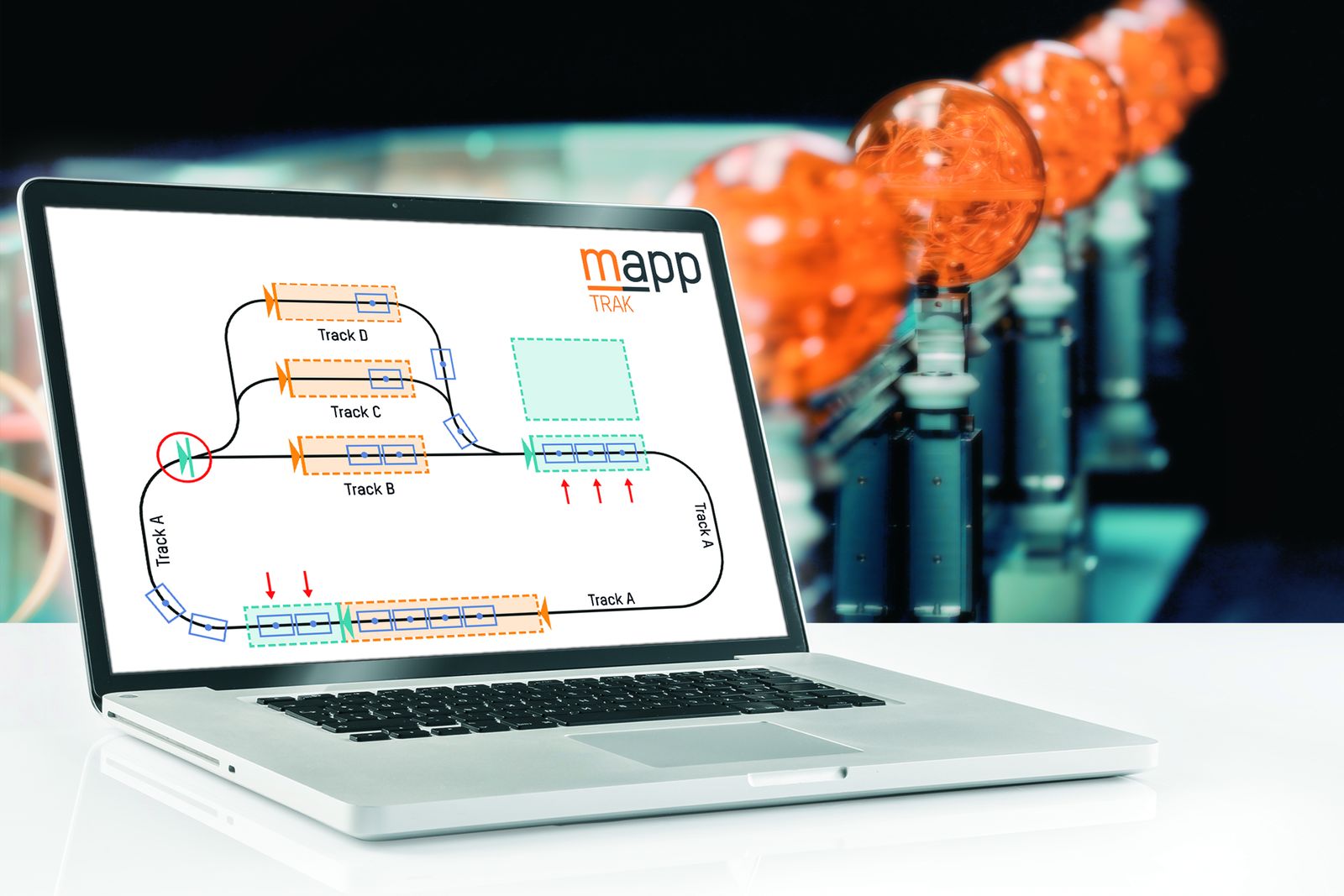
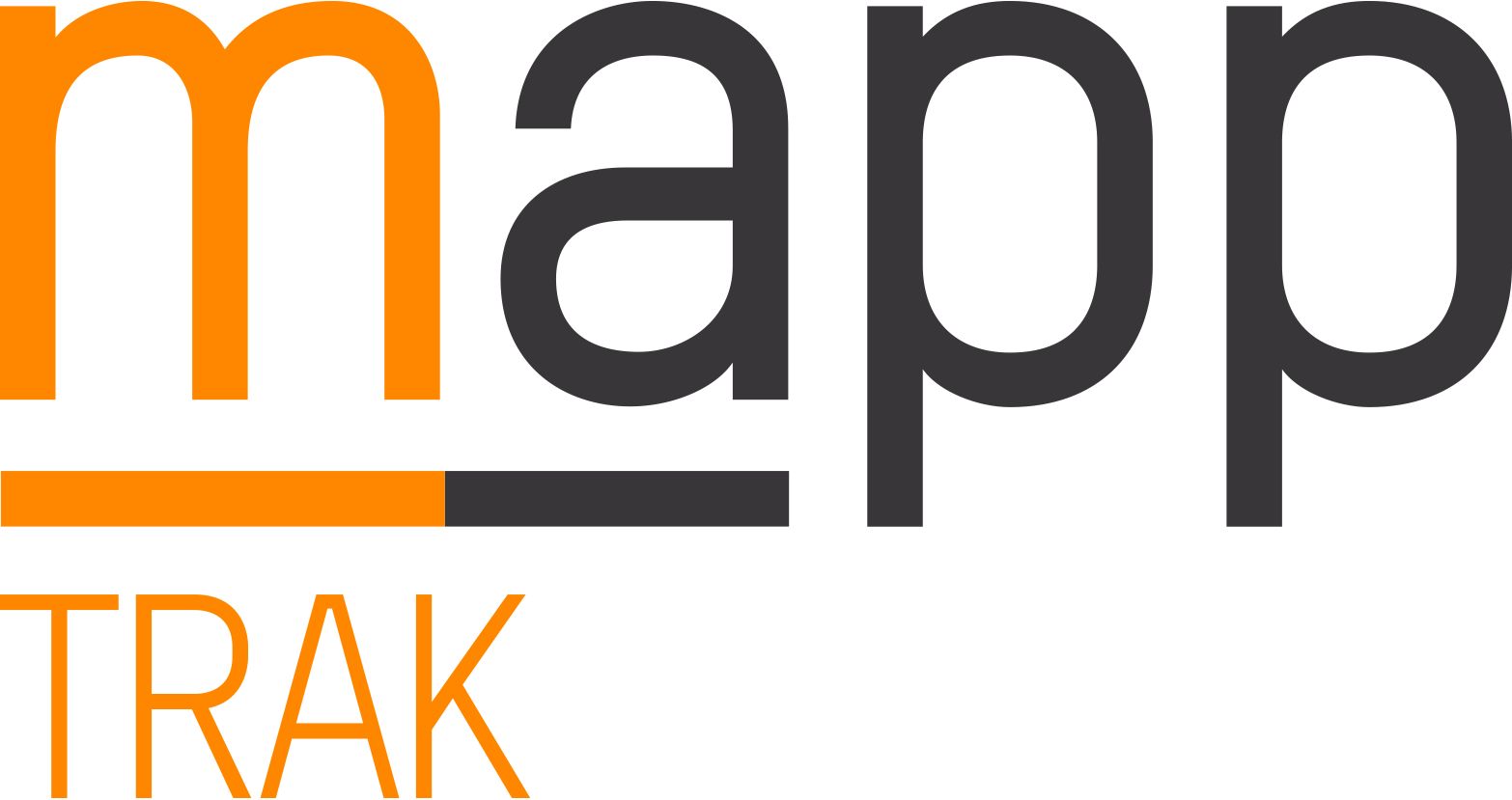
Le système de transport ACOPOStrak a justement été conçu pour offrir cette flexibilité. Sa structure modulaire, ses quatre éléments de base et sa fonctionnalité d'aiguillage intégrée permettent non seulement de réaliser quasiment toute forme de circuits, mais aussi d'adapter ou étendre ces circuits à tout moment. Les navettes sont contrôlées électromagnétiquement et indépendamment les unes des autres, même lorsqu'elles se trouvent de part et d'autre d'un aiguillage.
L'architecture dimensionnable du système permet de réaliser des circuits longs de plus de 100 m et parcourus par des centaines de navettes. Et pourtant : "malgré son inhérente complexité, le système est simple à manipuler," explique Robert Kickinger, Manager Mechatronic Technologies chez B&R. B&R
a simplifié le travail d'ingénierie nécessaire pour réaliser des solutions ACOPOStrak. Fabricants de machines et entreprises manufacturières peuvent ainsi mettre leurs produits sur le marché dans des délais très réduits. "Lorsque l'effort d'ingénierie est minime et lorsque les coûts associés diminuent, le retour sur investissement est plus rapide," ajoute R. Kickinger.
Collision impossible
Le logiciel système mapp Trak fourni avec le système ACOPOStrak rend toute collision impossible. "Ce logiciel est l'œuvre de nos développeurs les plus chevronnés," explique le spécialiste en mécatronique. Ces derniers ont réalisé avec maîtrise toutes les tâches mathématiques complexes qui sous-tendent les fonctionnalités clé du système.
Parmi ces fonctionnalités figurent l'évitement de collisions, la décomposition et la fusion de flux de produits à pleine vitesse, ou encore le calcul du meilleur chemin. Libérés de ces tâches, les développeurs d'applications gagnent un temps précieux.
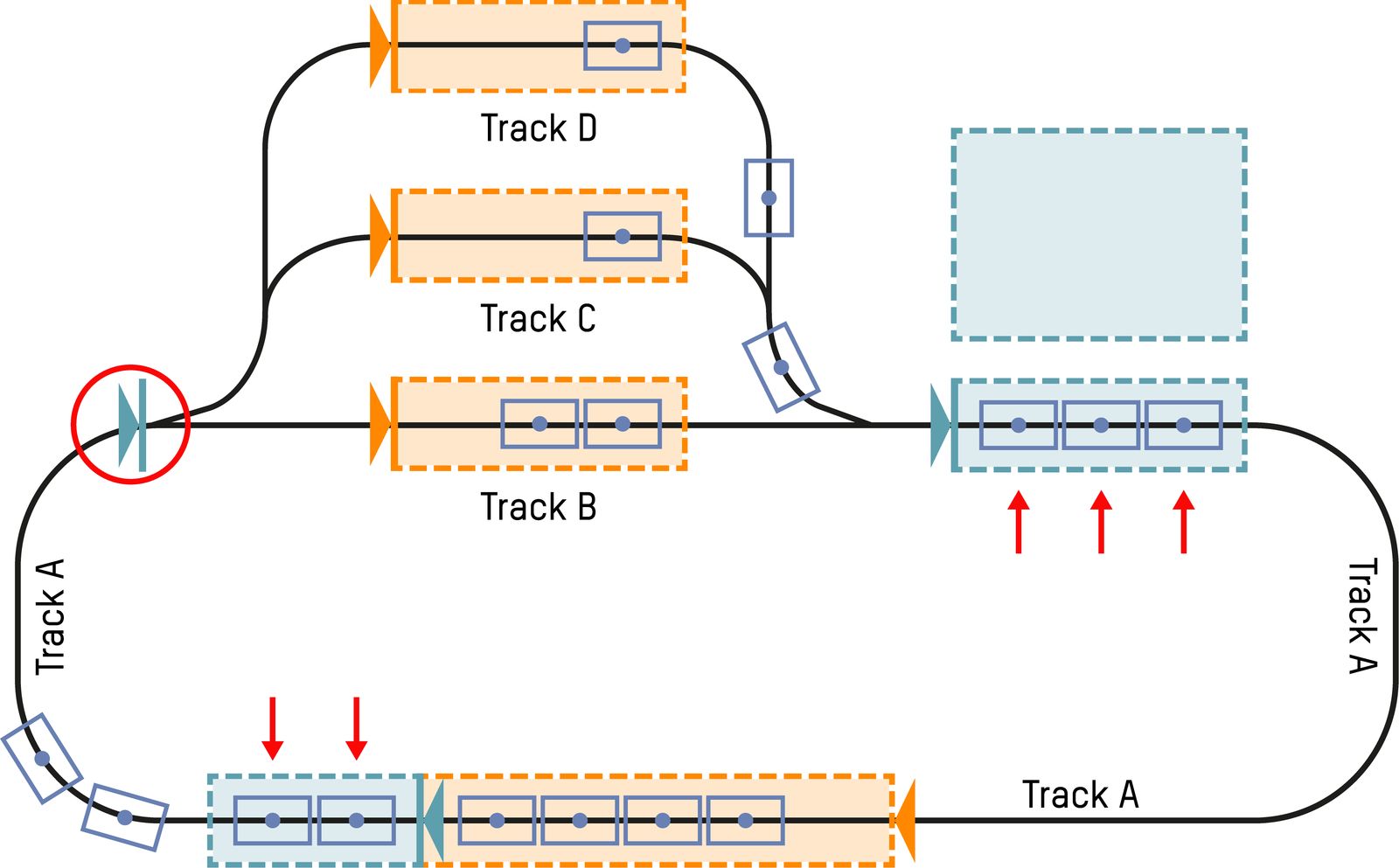
Même avec des produits de taille et de poids différents, aucune collision ne peut se produire. La taille du produit peut être configurée manuellement ou mesurée avec des capteurs. mapp Trak adapte ensuite le contrôle des navettes pour éviter toute collision.
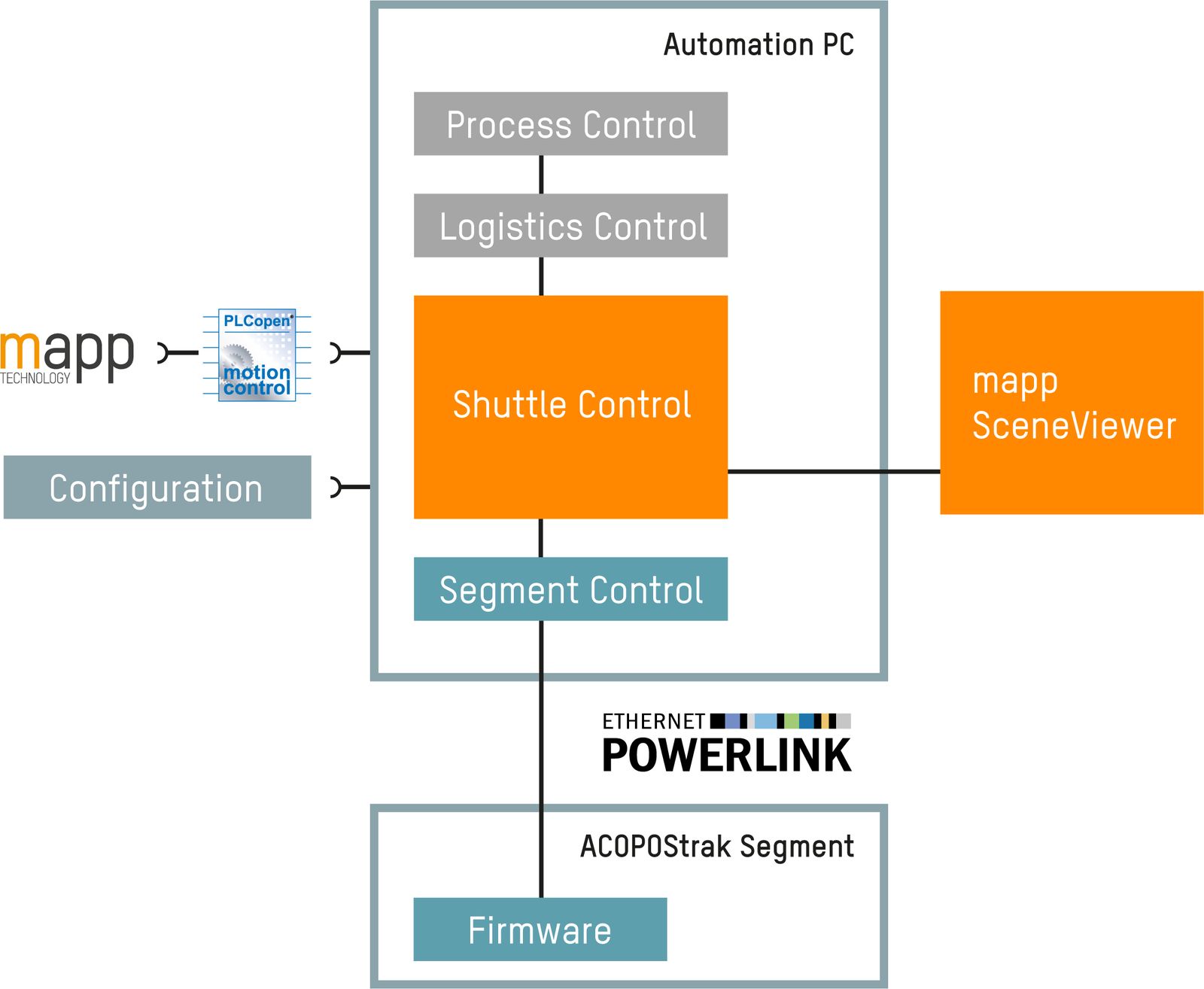
Programmation orientée process
Un autre facteur contribue à la simplification de l'ingénierie : la programmation orientée process. Avec mapp Trak, l'ingénieur logiciel décrit des règles dictant la manière dont les navettes doivent se comporter sur la piste. Ces règles deviennent actives quand les navettes passent des points de déclenchement virtuels sur la piste. Cette méthodologie basée sur des machines d'état permet une implémentation efficace des séquences de mouvements.
Aucun axe ni profil de mouvement ne doit être programmé individuellement pour chaque navette. Dans des cas où les navettes se comptent par centaines et où les chemins possibles sont multiples, cela prendrait bien trop de temps. La programmation orientée process offre aussi un autre avantage : celui de permettre le retrait ou l'ajout de navettes sans nécessiter le moindre changement dans le programme applicatif.
Simulation pour un fonctionnement efficace
La simulation intégrée dans mapp Trak permet de s'assurer visuellement que le fonctionnement du système est fluide. Les développeurs de l'application peuvent utiliser cette simulation pour tester le système et déterminer avec combien de navettes et à quelle vitesse l'application atteint une productivité maximale. "Avec leur PC bureatique, ils peuvent simuler de nombreux scenari sans les contraintes et les risques inhérents à un système réel," souligne Davide Migliorisi, Product Manager Track Systems chez B&R. Le logiciel dans la simulation est identique au logiciel système utilisé ensuite sur le contrôleur. Il est à tout moment possible de passer de la simulation au fonctionnement réel et vice-versa.
Par ailleurs, Scene Viewer permet de visualiser les interactions des navettes avec d'autres éléments mécaniques comme, par exemple, des visseuses, des étiqueteuses, ou des robots. Il suffit pour cela d'importer un fichier STEP de l'élément machine concerné et de modéliser le mouvement de cet élément dans le temps et dans l'espace. Ainsi, le développeur de l'application peut simuler le comportement des navettes ainsi que leurs interactions avec d'autres éléments machine. "L'aspect pratique qu'offre la simulation via mapp Trak est très apprécié de nos clients," confirme D. Migliorisi.
"L'interaction avec des éléments mécaniques externes fonctionne très bien car ACOPOStrak porte en lui les gènes des servovariateurs de la famille ACOPOS," dit-il. Les servovariateurs ACOPOS présentent des fonctions sophistiquées pour le contrôle des systèmes mono-axe et multi-axes, avec notamment des options étendues pour le couplage d'axes.
Les navettes peuvent être ainsi coordonnées avec des axes pilotés par des servovariateurs ACOPOS moyennant l'utilisation de commandes PLCopen, puis affichées sous la forme d'un jumeau numérique dans Scene Viewer.
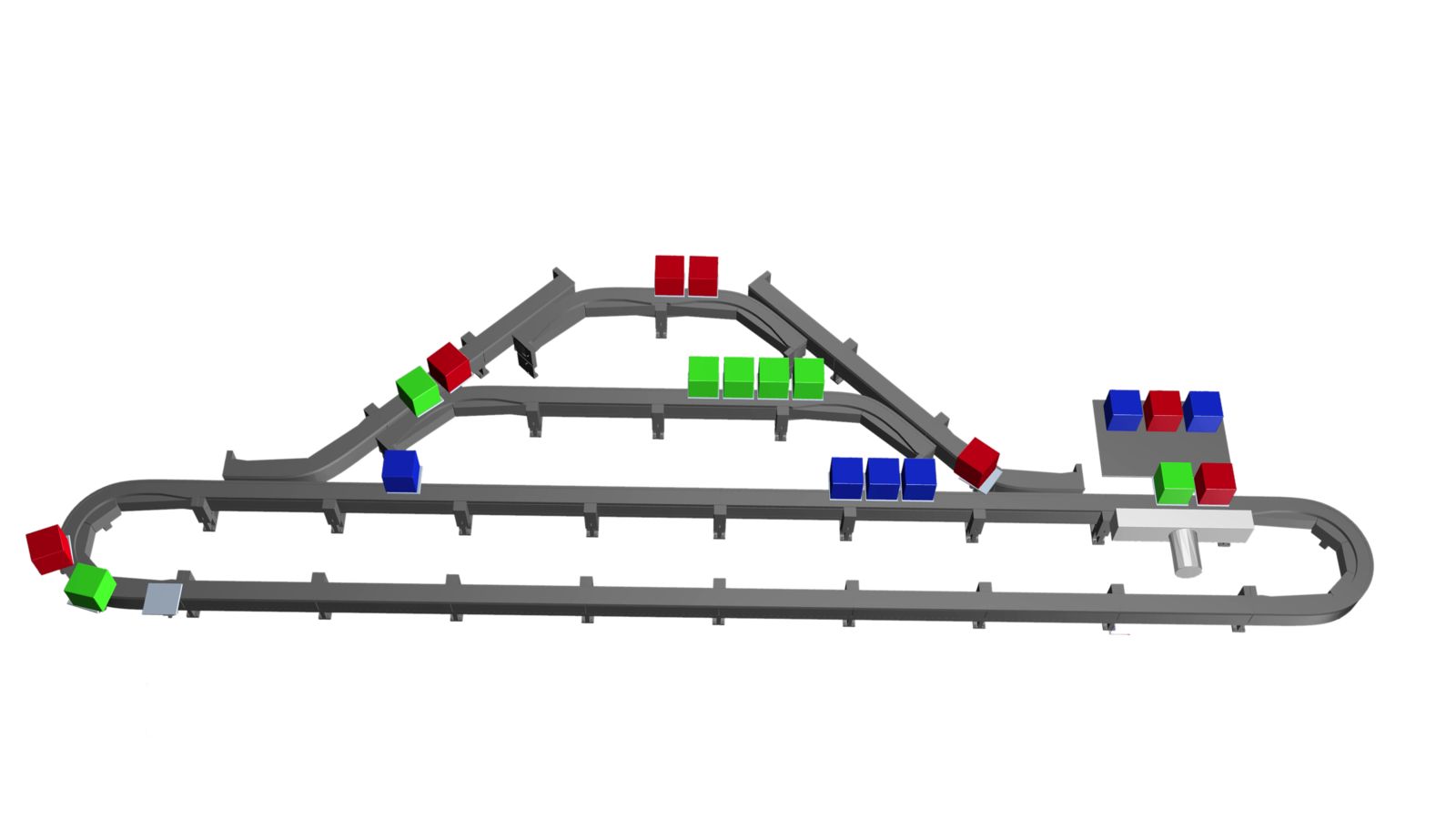
Flexibilité maximale
Des clients confirment déjà la simplicité d'utilisation du système ACOPOStrak. "Chez un client, le développement logiciel consécutif à l'extension d'une machine existante avec des segments linéaires ACOPOStrak additionnels n'a pris que quinze minutes", rapporte R. Kickinger. "La machine a été ensuite remise en marche immédiatement". Le concept de programmation découplée du matériel conçu pour l'ACOPOStrak montre ici toute sa puissance.
Le logiciel système mapp Trak permet de relier les données produit à la navette sur laquelle se trouve le produit correspondant. "Les utilisateurs bénéficient ainsi d'une flexibilité maximale," assure R. Kickinger. Un enregistrement de données spécifique à un produit sur une ligne pharmaceutique peut ainsi contenir la composition exacte du principe actif ainsi qu'un identifiant produit unique. De plus, il est aussi possible d'enregistrer à quelle date et à quelle heure le produit passe dans chaque station de traitement. L'ingénieur d'application peut ainsi réaliser un système de tracking conforme à la FDA.
Un système complexe facilement maîtrisable
mapp Trak garantit trois choses : l'absence de collisions entre navettes, le non-franchissement de barrières virtuelles, et le respect des limites configurables de vitesse. Ces garanties alliées à la simplicité de programmation et à la simulation intégrée facilitent énormément la prise en main du système ACOPOStrak pour l'utilisateur. L'introduction de nouveaux produits, toutes tailles de lot confondues, s'effectue ainsi rapidement et moyennant un minimum d'efforts. Cette flexibilité est cruciale pour remporter des commandes à honorer rapidement.
Auteur : Carmen Klingler-Deiseroth, journaliste freelance
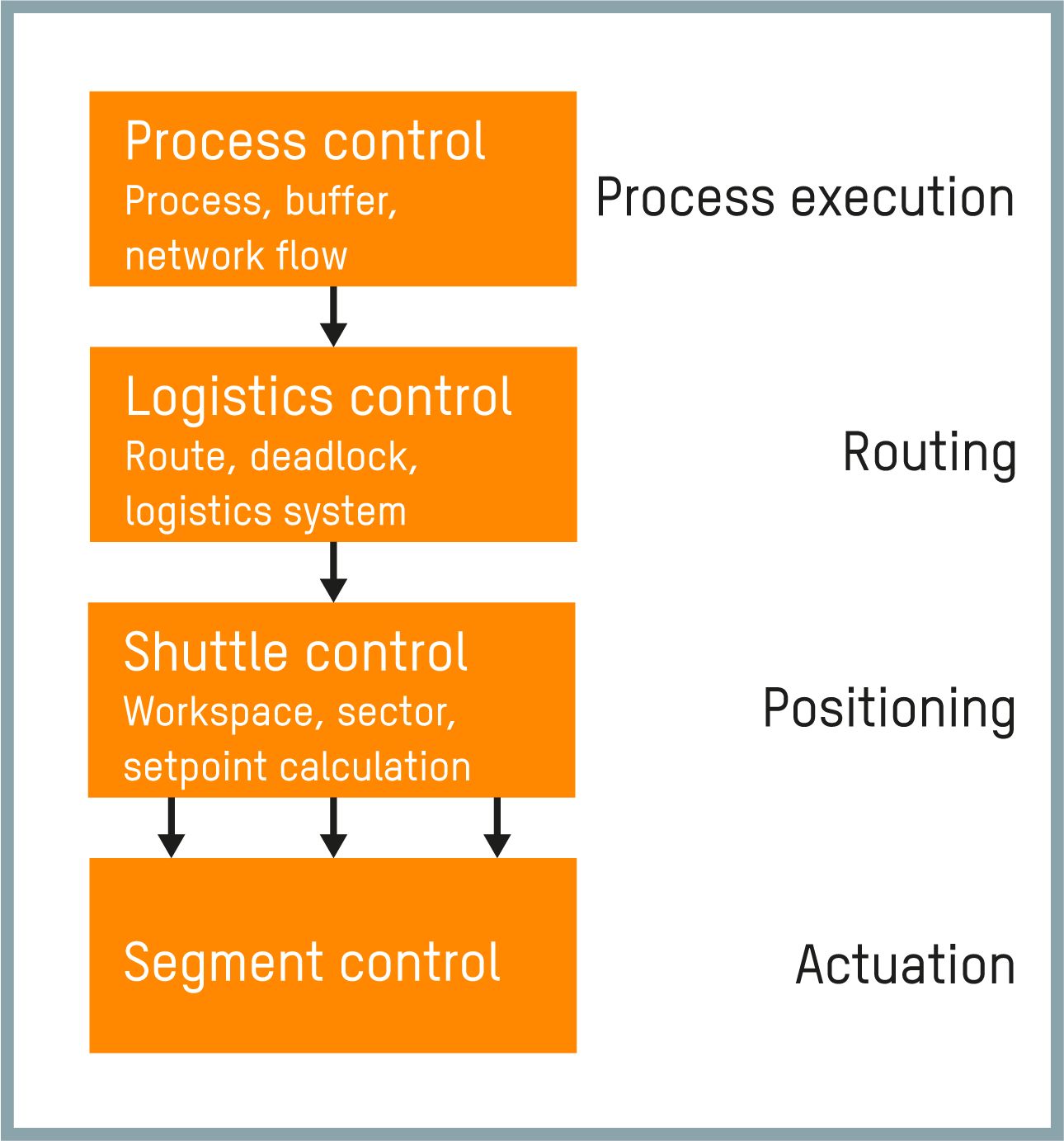
L'architecture de mapp Trak
L'architecture logicielle de mapp Trak se divise en quatre niveaux principaux. Le niveau le plus bas appelé Segment Control contrôle le mouvement des navettes sur les segments.
Le niveau immédiatement supérieur appelé Shuttle Control est celui où sont calculées les consignes de position pour les navettes. Si l'ingénieur d'application souhaite coupler des navettes en utilisant par exemple des blocs de fonction PLCopen, c'est également à ce niveau que cela est réalisé. Le niveau Shuttle Control gère également les ajouts et les retraits de navettes sur la piste, par exemple lorsque l'ACOPOStrak est utilisé en combinaison avec des convoyeurs classiques, ou lorsque des navettes sont introduites ou retirées par des humains ou des robots.
Le troisième niveau appelé Logistics Control est celui où le routage des navettes d'une station de traitement à l'autre est automatisé.
Le quatrième niveau est dédié au contrôle du process. Ce niveau fournit à l'ingénieur d'application l'interface de programmation nécessaire pour décrire les flux de produits.