Excess heat generated in control panel enclosures must be dissipated or removed to keep electronic components functioning reliably. But how sure are you that your cooling system is doing its job? A new I/O module from B&R's X20 series puts uncertainty to rest. It monitors environmental conditions in the control cabinet without needing any additional sensors.
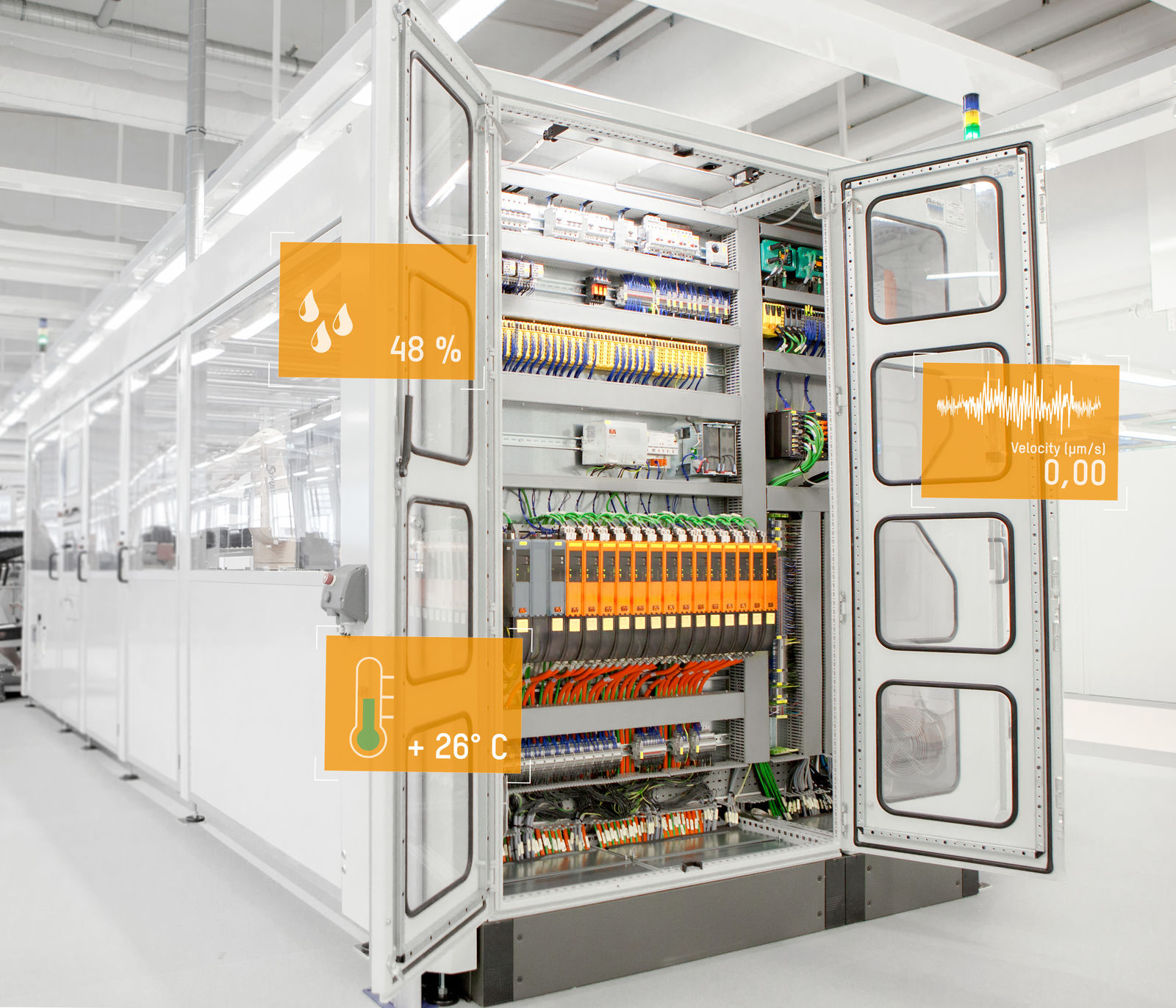
High temperatures, humidity and vibrations are unwelcome guests in electronics enclosures. Without sufficient cooling, the likelihood of malfunctions and failures rises right along with the temperature. In the worst case, it could bring down an entire production line and cause substantial unplanned costs.
Particularly tricky are those situations that only occur sporadically. Like when the sun shines through the production hall window every day at noon and overheats the cabinet. In such cases, cabinet monitoring provides service technicians with meaningful data to help them figure out what's going on.
Plug-and-monitor
Installing a dedicated condition monitoring box in the control cabinet involves cost and effort. Not only do you have the cost of the hardware, it also needs to be wired and configured to communicate with the control application. The added overhead causes many to shy away from a solution. But there is an easier way.
B&R proves that with its X20CMR011 I/O module. The module is mounted on the DIN rail just as easily as any other module and immediately feeds condition data into the control application. Whether it's an existing B&R-automated machine or a new one, there is no extra wiring or any other hardware required. In larger enclosures, additional modules can be placed at strategic locations and communicate with the PLC via a bus controller.
Onboard logger
The monitoring module tracks temperature and humidity, and an integrated accelerometer also measures vibrations. The control application can read this data at any time for alarms or service documentation.
The module's built-in memory can store key data, such as minimum and maximum values or time spent within a defined range. This memory functions without a battery and is therefore maintenance free, and the data remains available even if the PLC is replaced.
But that's not all the module can do. It also has two digital inputs for connecting external sensors – like contacts that tell you when the cabinet door is open. For external temperature sensors, there are also two PT1000 inputs. A digital output lets you connect an indicator light that draws immediate attention in the event that excessive temperatures, moisture or vibration are at risk of damaging the electronics in the cabinet.
Low overhead, big benefits
The cabinet monitoring module keeps overhead to a minimum while offering substantial benefits. Electrical and electronic components are well protected, because harmful temperatures, humidity and vibrations are reliably detected.
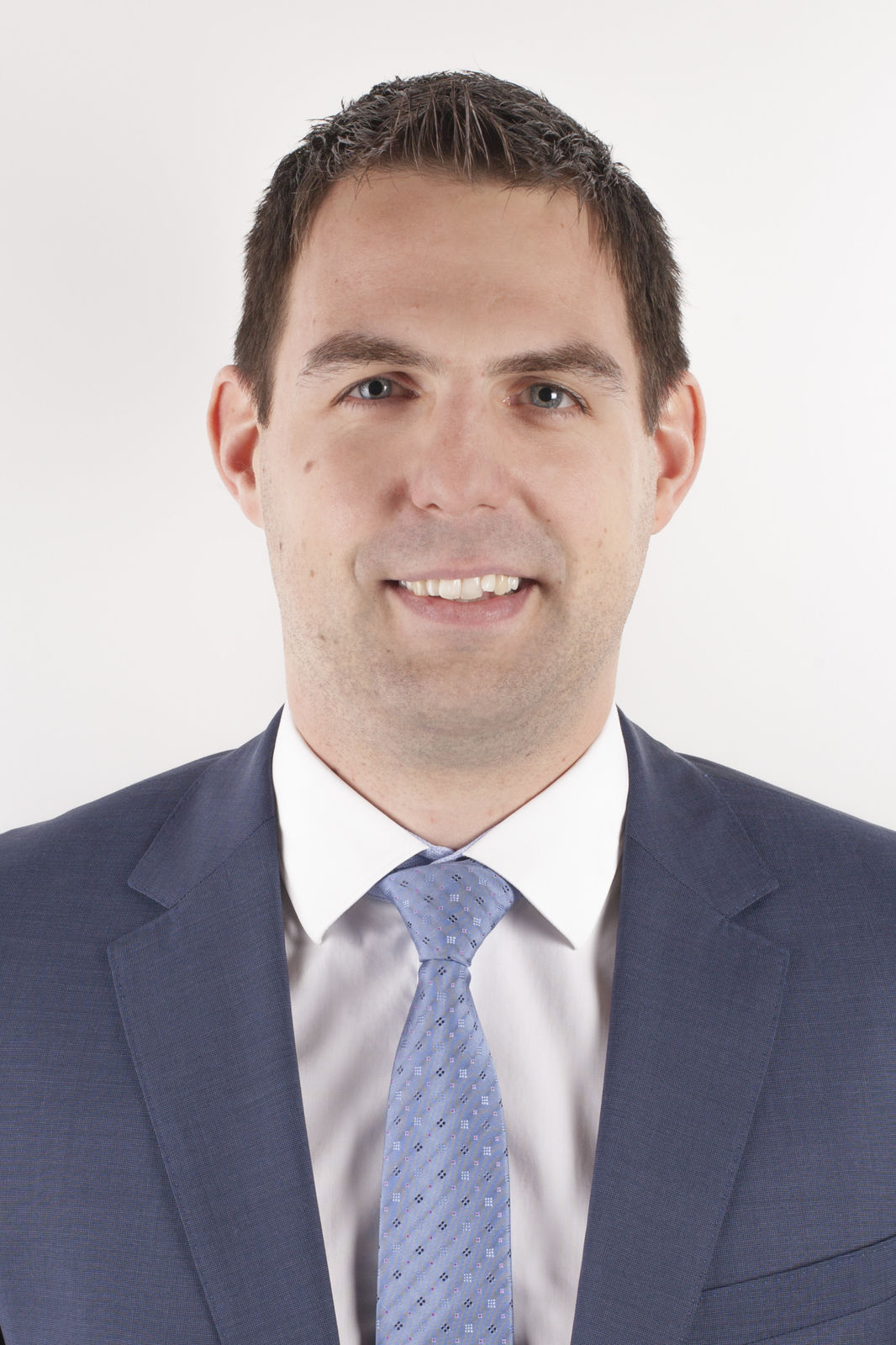
Control cabinet monitoring doesn't only benefit the user of the machine, however. The machine builder can also gain valuable information. They can track the real-world conditions under which their cabinets are being operated, including the prevailing temperature and humidity, as well as how frequently the cabinet door is opened. That enables them to recommend proactive maintenance measures and make targeted product improvements.
A worthwhile investment
Last but not least, it becomes much easier for the machine builder to deal with warranty claims. The stored data makes it possible to determine quite clearly if operator error is to blame – for example if the cabinet door was constantly left open, preventing the air conditioning from functioning effectively. The small investment in the monitoring module pays off by empowering the machine builder to quickly and easily deny an unjustified claim.
Author: Andreas Hager, Product Manager - Control Systems, B&R
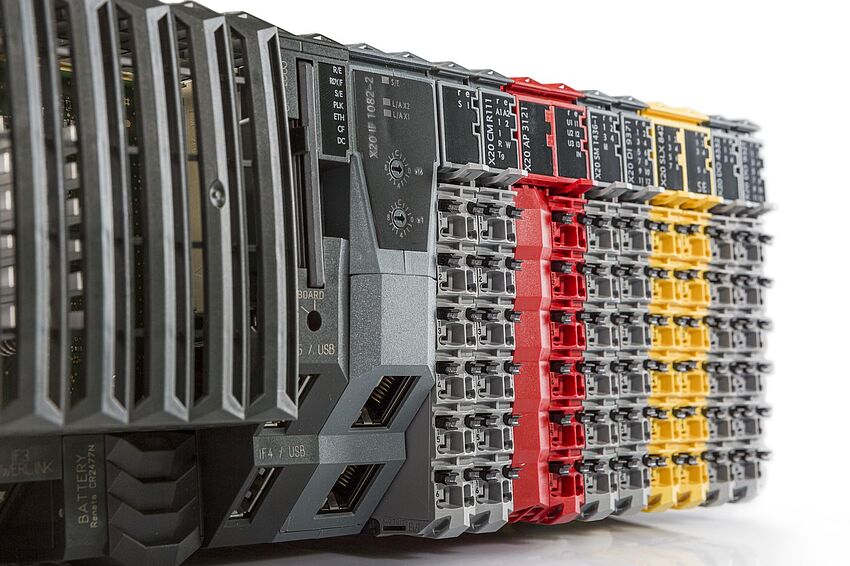
The X20 control and I/O system is fully flexible, scalable and modular. It covers nearly all conceivable requirements for cabinet-based controls. The portfolio ranges from very compact devices for simple control tasks to high-performance PLCs able to handle complex algorithms and even robotics applications.
With a convenient plug-in design, interface cards for all common communication protocols and a wide portfolio of I/O modules can be added to the X20 PLCs. Safety controllers and safe I/O modules integrate seamlessly into the X20 system. The I/O slices have a three-part design – terminal block, electronics module and bus module – which makes them economical, easy to handle and simple to install. The X20 system is ready for OPC UA FX and is therefore future proof.