Pour les produits alimentaires ou pharmaceutiques sous emballage hermétique, les tests d'étanchéité sont une étape critique du process de production. Oxipack a développé une unité d'inspection qui détecte les fuites à l'échelle microscopique sans altérer le produit. Grâce à l'étroite coopération entre le fabricant de machines Geurtsen et les experts en technologies de contrôle de B&R, cette unité est maintenant suffisamment efficace pour tester chaque article parcourant la ligne.
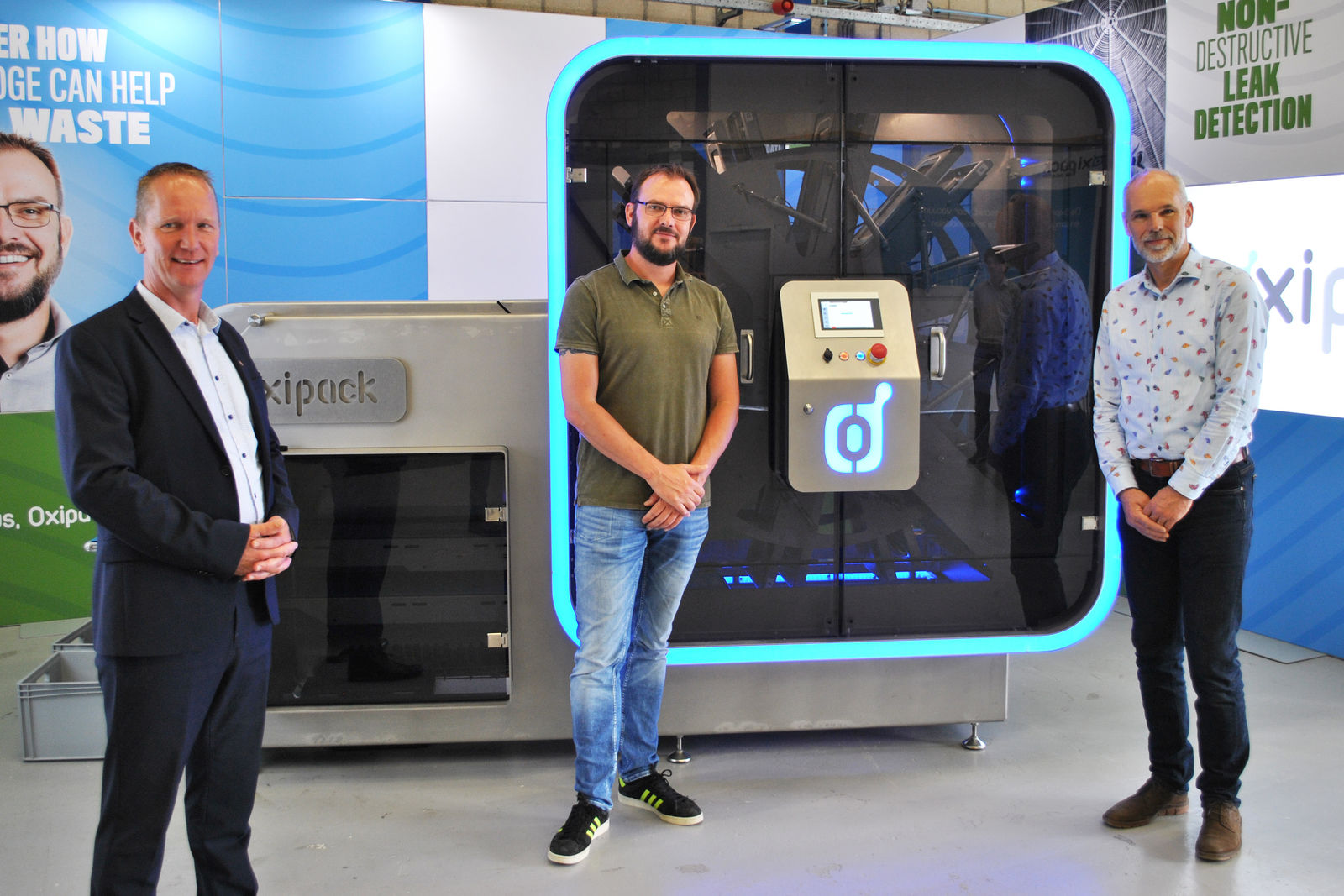
Dans leur quête perpétuelle de réduction de déchets et d'amélioration de la qualité, les entreprises des secteurs agroalimentaire et pharmaceutique attachent une grande importance aux emballages. Un de leurs principaux objectifs est de retirer du process le plus tôt possible les emballages qui fuient. Bien souvent, cette opération consiste à immerger des échantillons aléatoires dans l'eau et à regarder si des bulles d'air s'échappent. Cependant, ces tests manuels ne sont pas assez fiables et précis pour détecter des trous microscopiques. Les microfuites sont si petites qu'elles ne sont pas détectées lors de ces tests. Pourtant, elles n'en restent pas moins suffisamment grandes pour altérer le produit ou même présenter un risque pour la santé des consommateurs.
Oxipack Leak Detection a développé une méthode de test alternative basée sur la technologie du vide. "Le principe est simple," relate Pim Jobse, directeur technique de l'entreprise basée à Houten aux Pays-Bas. "Vous placez le produit entre deux membranes en caoutchouc puis scellez le tout dans une chambre que vous mettez ensuite sous vide. Si l'emballage est hermétique, rien ne se passe. En revanche, si l'emballage présente un trou, la pression dans la chambre augmente. Cette méthode permet de détecter des fuites de très petite taille (jusqu'à dix micromètres) sans souiller ni contaminer l'emballage. Ce procédé permet en outre de tester chaque produit.
À l'instar de l'immersion dans l'eau, la détection par le vide prend aussi du temps. "L'ensemble du processus dure environ une demi-minute," explique P. Jobse. Ceci a confronté les ingénieurs d'Oxipack à un vrai défi. Comment, dans ces conditions, tester 120 unités par minute et répondre ainsi aux besoins du marché ? L'entreprise s'est donc mise à la recherche d'un fabricant de machines capable de développer une solution lui offrant l'efficacité nécessaire et présentant la plus petite empreinte possible.
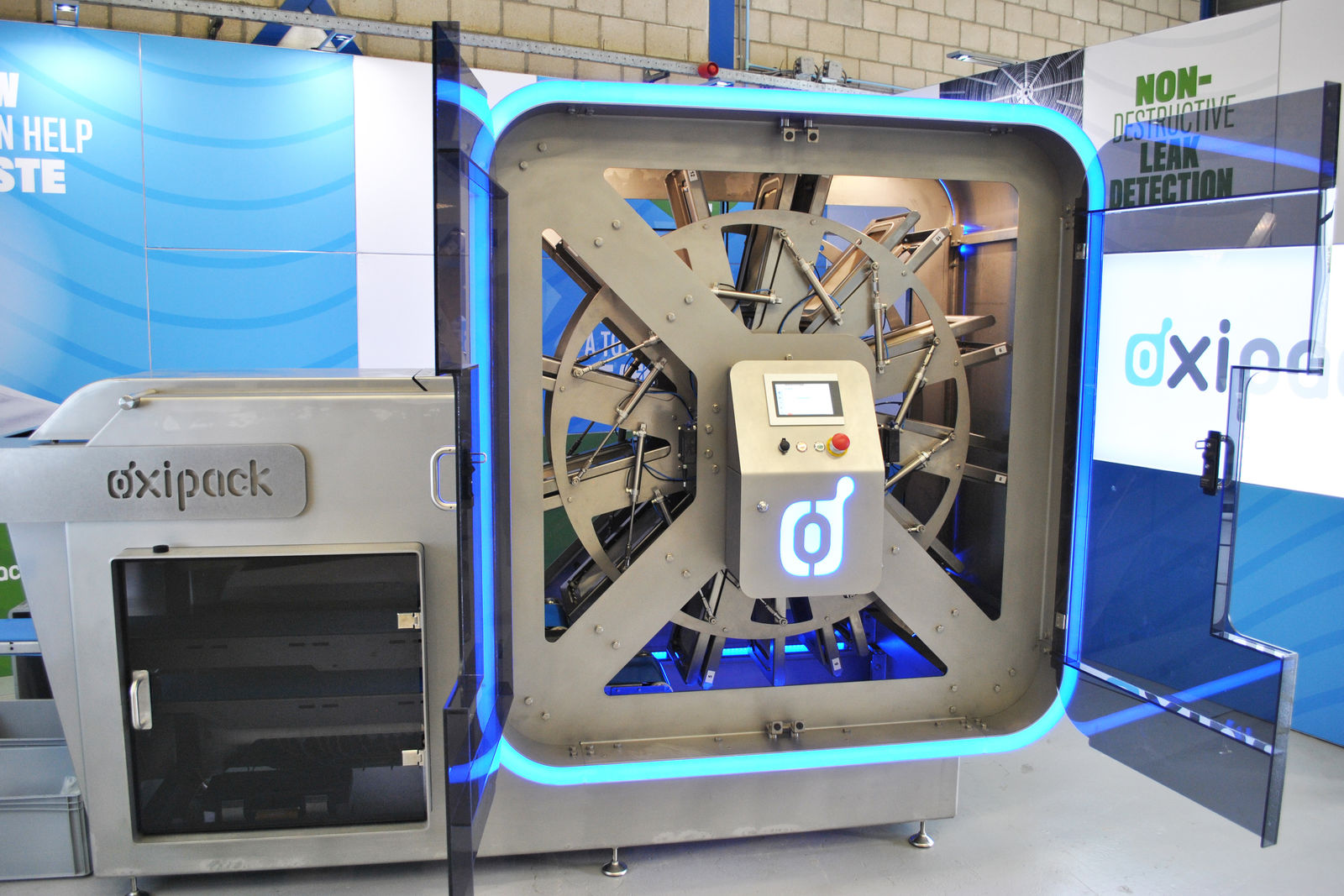
Environnement de développement universel
Partenaire de longue date d'Oxipack, le fabricant de machines innovant Geurtsen a fait le choix d'utiliser la technologie de contrôle de B&R, une technologie dont il a standardisé l'utilisation il y a plusieurs années, "notamment en raison de la facilité avec laquelle tout peut être programmé et contrôlé avec l'environnement de développement Automation Studio de B&R," révèle Wardo Dietrich, Chief Designer chez Geurtsen. "Quoi que vous connectiez au système, la communication s'effectuera sans problème. Pouvoir tout faire dans un environnement qui m'est familier est pour moi un vrai plus."
"J'ai été convaincu en une dizaine de minutes," rapporte P. Jobse. Impressionné par la facilité avec laquelle des réponses ont été trouvées à chacune de ses questions, le directeur technique l'a été aussi par les fonctions de diagnostic du contrôleur. "L'état du contrôleur s'affiche immédiatement sans qu'il soit nécessaire de faire quoi que ce soit ; tout est préprogrammé. Chez d'autres fabricants, quand vous recevez par exemple une erreur relative à un driver, c'est à vous de trouver et de résoudre le problème. Avec le System Diagnostic Manager de B&R, vous disposez d'un outil qui affiche des informations détaillées et propose une solution."
Réduire l'encombrement
Oxipack avait des attentes claires envers les développeurs de Geurtsen. "En raison d'expériences non probantes dans le passé, j'avais comme instruction de ne pas développer de carrousel," rapporte W. Dietrich. Le responsable de Geurtsen a ainsi exploré plusieurs concepts comme, par exemple, celui de disposer des chambres sous vide comme des livres sur une étagère pendant les tests. Finalement, toutes ces idées se sont révélées trop coûteuses et une seule option s'est alors imposée : celle d'un carrousel... Mais à la différence du carrousel horizontal qu'utilisait Oxipack précédemment, W. Dietrich a nettement réduit l'empreinte nécessaire en basculant le carrousel à la verticale.
Prénommée The Rotary, la nouvelle machine d'inspection contient jusqu'à douze chambres de test. Une fois le produit introduit dans la chambre, cette dernière se ferme, l'air qu'elle renferme est évacué, et le test d'étanchéité est effectué. Ainsi, lorsque l'emballage retourne à son point de départ, la machine sait si celui-ci est étanche ou s'il doit être rejeté. Les emballages conformes glissent ensuite sur le tapis de convoyage correspondant.
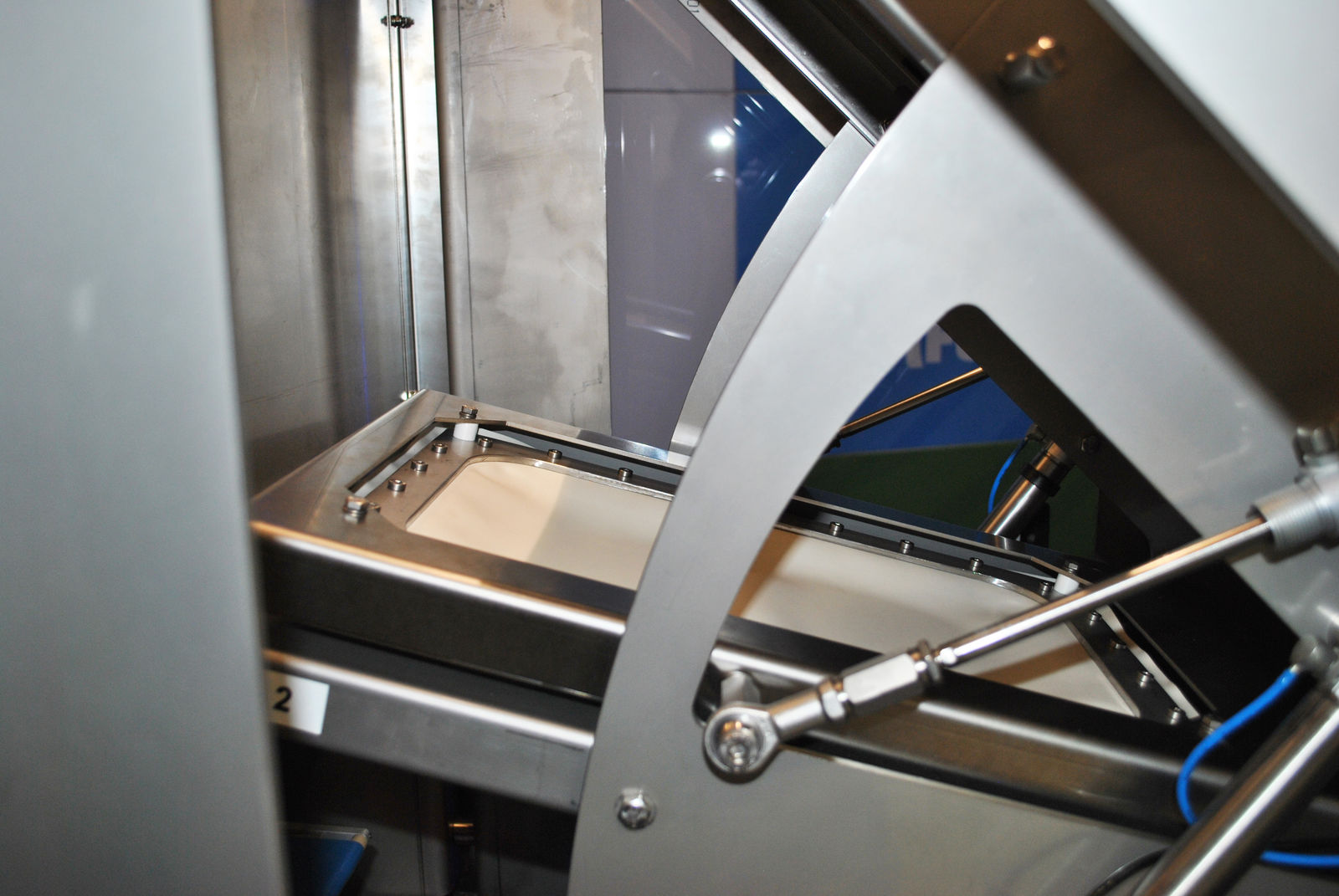
Pour l'amenage des emballages, Geurtsen a choisi un convoyeur constitué de navettes effectuant un mouvement arrière au dernier moment alors même que le tapis de convoyage continue d'avancer. "Ceci permet de faire tomber le produit en douceur et à la position voulue dans le carrousel," explique W. Dietrich. "Nous utilisons souvent cette méthode. Néanmoins, avec une roue en rotation, le timing est très serré." Les nombreux tests réalisés dans le cadre de la collaboration entre Geurtsen et B&R ont permis d'aboutir à une solution optimale.
Le tapis d'amenage et le carrousel sont parfaitement synchronisés grâce à un système entièrement intégré de B&R comprenant des servovariateurs, des variateurs de fréquence et des composants de sécurité. L'ensemble de l'installation est contrôlé par un Panel PC 2100 B&R incluant à la fois l'interface homme-machine et un automate puissant à base PC. "Grâce aux composants logiciels mapp de B&R, nous pouvons adapter le convoyeur à différents emballages sans effectuer de calculs compliquées. Il suffit simplement de régler quelques paramètres." En utilisant le composant mapp dédié à la gestion des recettes, les utilisateurs peuvent rapidement régler la machine pour passer à un produit de taille et de poids différents. Grâce à des capteurs déterminant automatiquement les paramètres du produit, ils peuvent même traiter simultanément plusieurs combinaisons de produits.
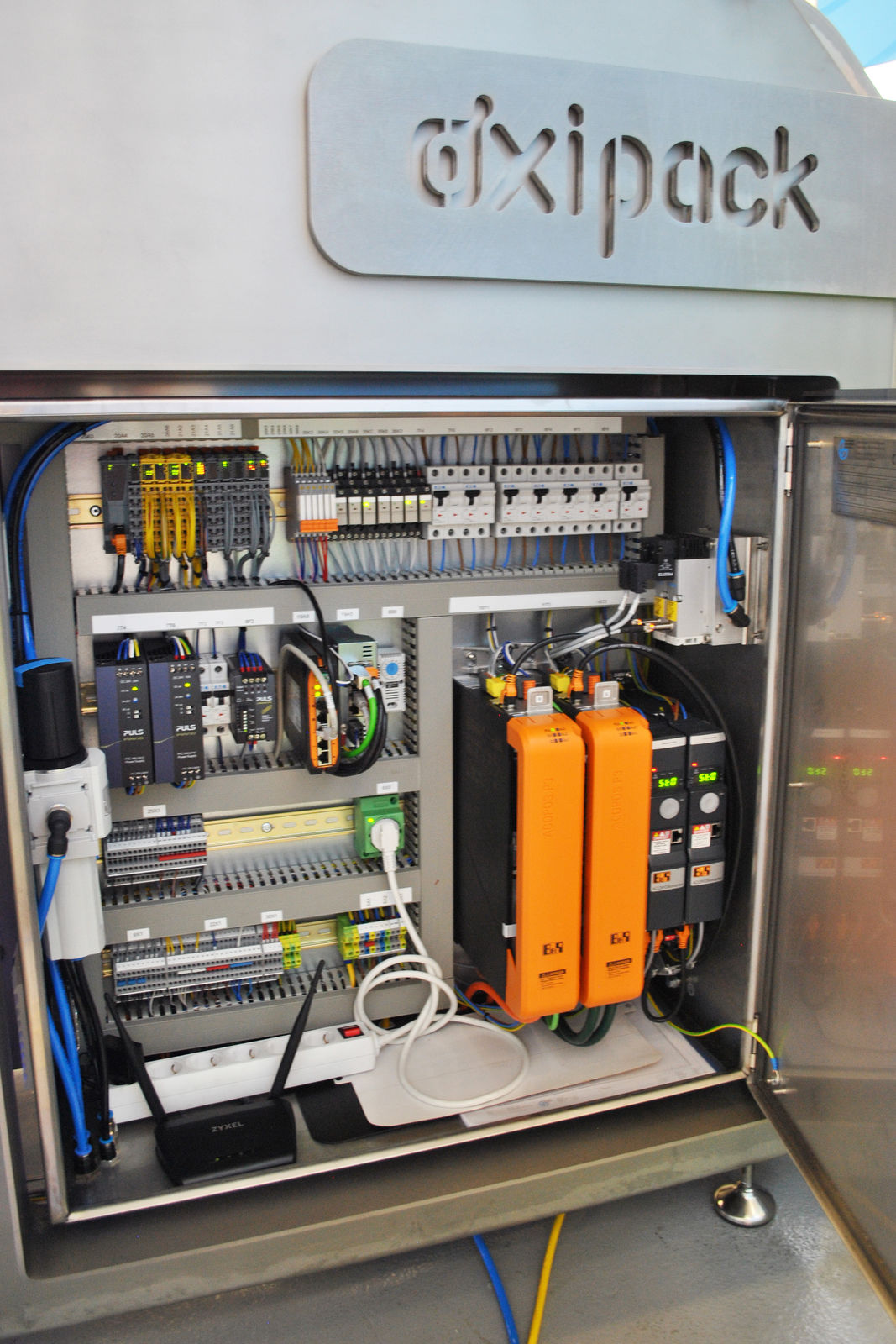
Échelonnable et compact
La première machine d'inspection réalisée par Oxipack et Geurtsen est partie chez un client italien pour y être testée. "Avec l'installation actuelle, ils peuvent tester 20 produits par minute," indique P. Jobse. Pour que le test des produits puisse être effectué en production, il faut atteindre une cadence de 120 emballages par minute. "C'est ici que la conception modulaire s'avère payante," note P. Jobse. "Le client peut facilement ajouter cinq roues supplémentaires sans incidence notable sur l'empreinte de la ligne d'emballage."
![]() | Wardo Dietrich Chief Designer, Machinefabriek Geurtsen "Nous utilisons la technologie de contrôle de B&R de manière standard depuis des années. Cela tient surtout à l'environnement de développement Automation Studio de B&R qui nous permet de tout programmer et contrôler facilement. Quoi que vous connectiez au système, la communication s'effectue sans problème. Pouvoir tout faire dans un environnement qui m'est familier est pour moi un vrai plus." |