In production environments where humans work in close proximity to machines, conventional sensors provide insufficient active protection against injury for operators. By integrating openSAFETY-based light grids into its automation landscape, B&R is opening up completely new approaches to safety for today's manufacturing facilities.
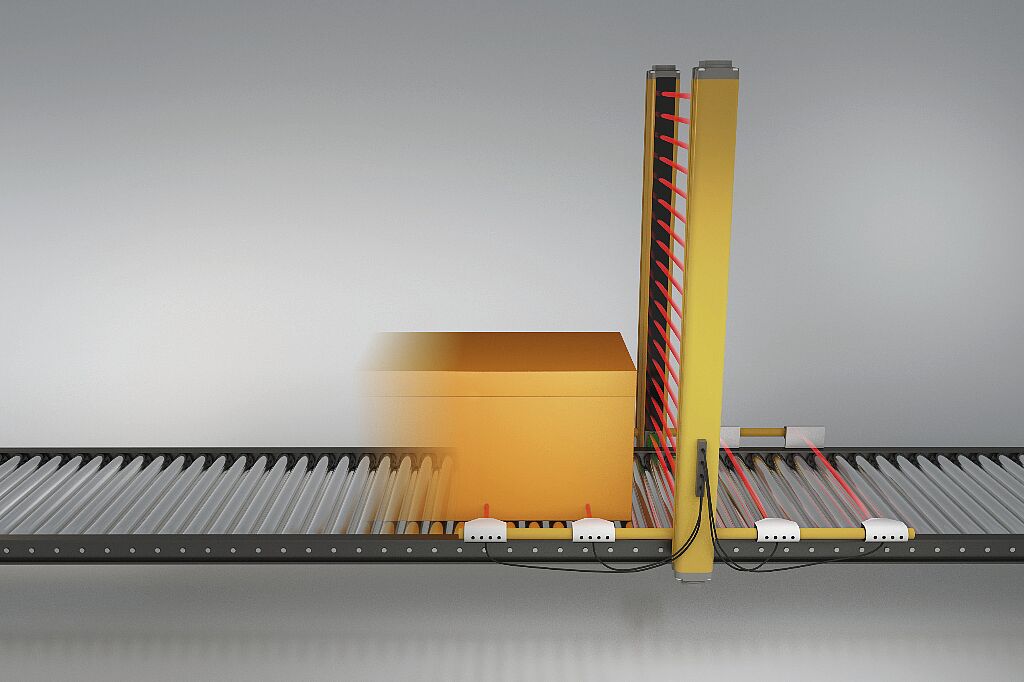
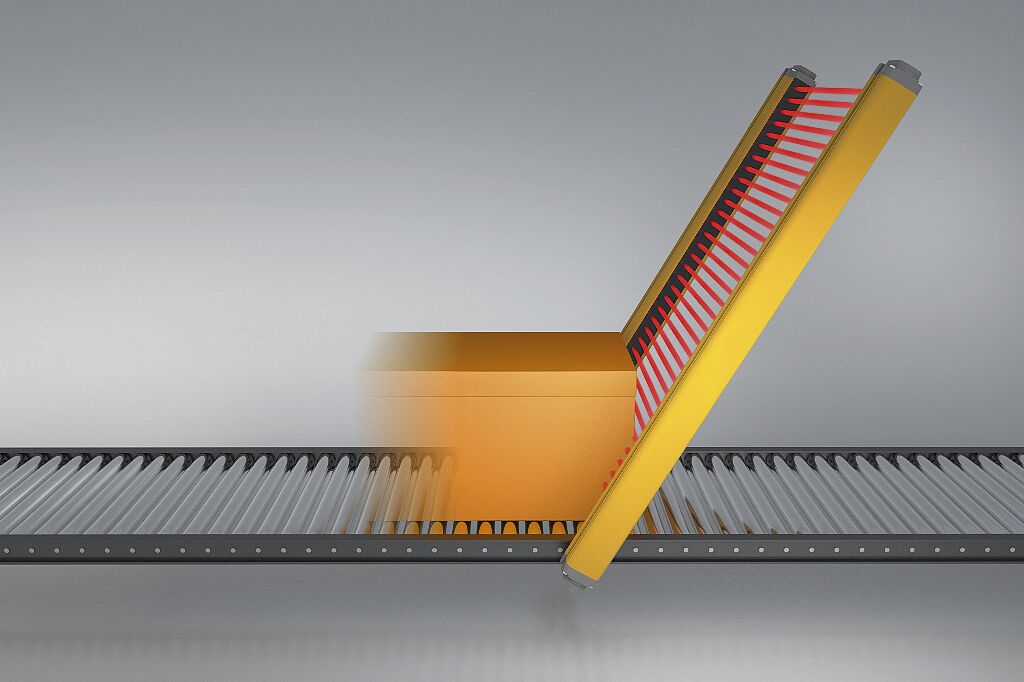
Light grids have been used for many years now to protect operators of machinery and equipment. "Unfortunately, conventional light grids are very inflexible," explains Miodrag Veselic, technology manager of openSAFETY at B&R. They are known to hinder the implementation of modern design concepts where human operators and machinery actually work together hand in hand.
It is for this reason that the EPSG developed an openSAFETY profile for intelligent light grids. "B&R is the first manufacturer to work on completely integrating this type of profile into its automation landscape," explains Veselic. The automation specialist is accompanied on this journey by the Italy-based company Datalogic, who is busy developing a light grid based on the new profile.
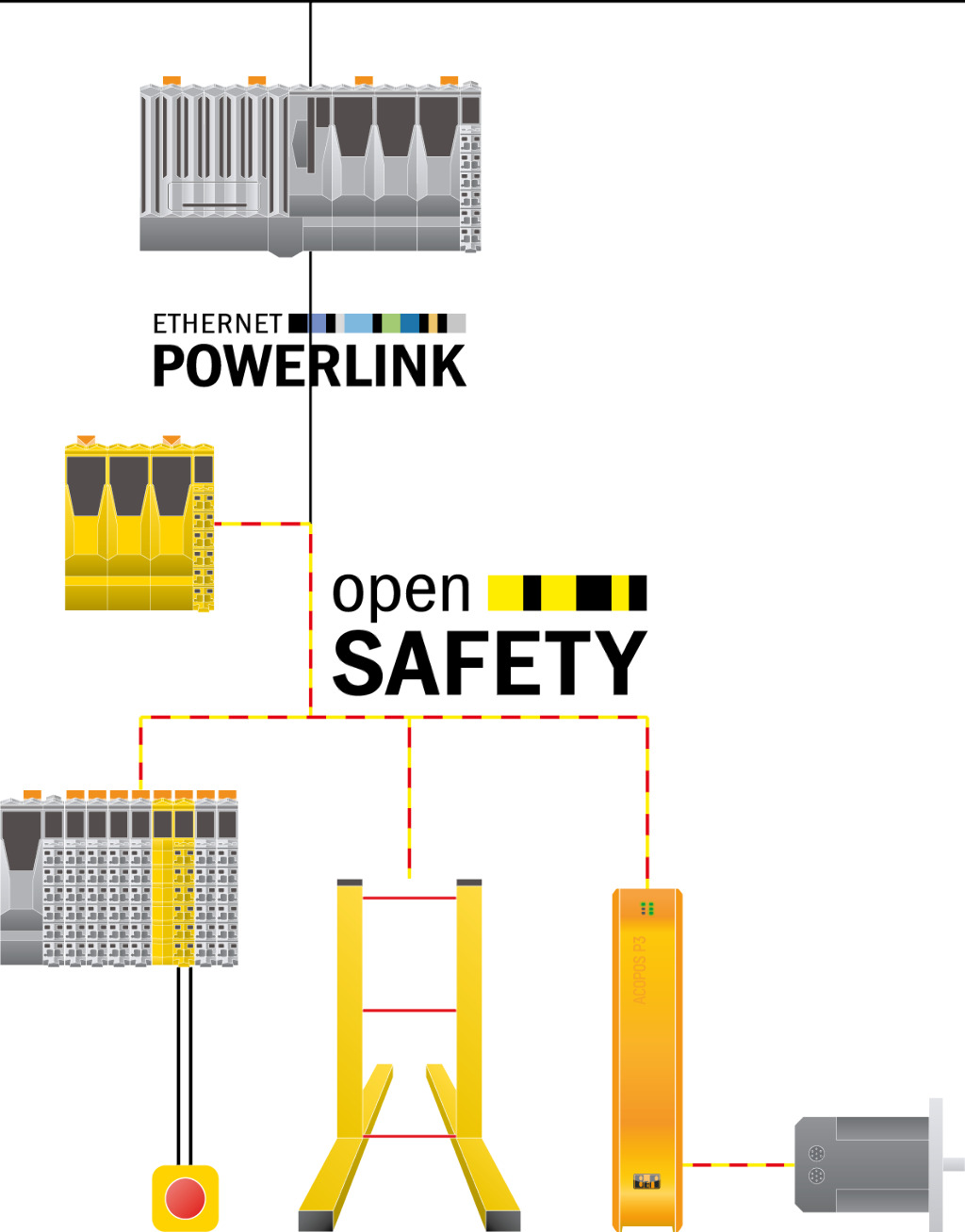
No hardwiring necessary
The intelligent light grid is connected directly to the real-time POWERLINK network. The overlying openSAFETY protocol replaces the hardwiring that used to be necessary for the light grid. "Since no safe I/O channels are necessary, an application with openSAFETY light grids is less expensive than a hardwired solution," explains Veselic.
Intelligent single-beam evaluation
Light grids with single-beam evaluation, as they are defined in the new EPSG profile, provide an easier way. "When this type of light grid is mounted at an angle, we are able to obtain all the data we need for intelligent muting," says Veselic. Based on which light beam is interrupted first, it is possible to determine the direction traveled by the product – without any additional hardware.
openSAFETY provides the SafeLOGIC controller with detailed information about which beam was interrupted and when. In addition to the product's direction of movement, it is also possible to determine its height – and, using the transport speed, its length as well.
Using this information, the safety controller is able to confirm that the product moving through the light grid is exactly the one that was expected. If a person were to sit on a product in order to bypass the photoelectric sensor, for example, then the machine would enter its safe state. "Solutions using conventional light grids require a lot of technical effort in order to detect that type of tampering," explains Veselic.
Programmed in the engineering software
With a B&R solution using openSAFETY light grids, safety functions such as muting and blanking are easily programmed in Automation Studio. Once an openSAFETY light grid has been installed and the node number set on the device, the rest of the configuration is handled in Automation Studio.
Conventional light grids require tedious DIP switch configuration on the device or even the use of dedicated software. This becomes even more problematic once everything is installed, because the DIP switches are difficult to reach and represent a potential source of errors.
Fast commissioning
"openSAFETY light grids considerably reduce the amount of work needed for commissioning – especially for equipment produced in series," explains Veselic. This is because, once written, the safety application can be reused on every machine. The light grid simply has to be connected to the network. The safety controller automatically detects whether it is dealing with the correct light grid model and transfers the configuration to the device. Errors that might otherwise result from manual configuration or on-site wiring are prevented.
"The troubleshooting possibilities of the intelligent light grid are a huge step forward as well," adds Veselic. Error messages that used to require painstakingly reading and interpreting LED blink patterns can now be viewed in plain text. This allows for more detailed diagnostics and considerably shorter downtime.
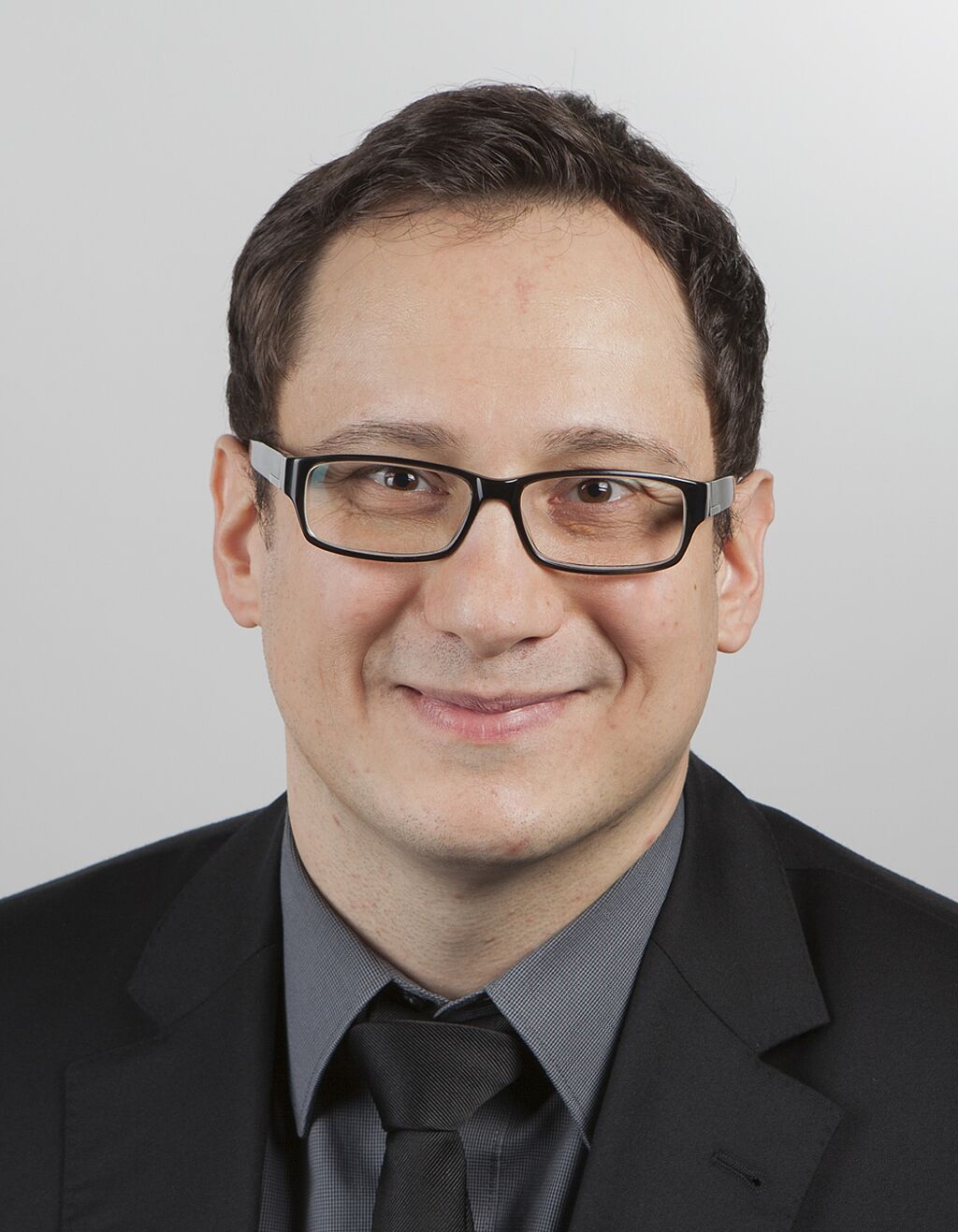
"The possibilities opened up by the openSAFETY light grid greatly simplify the cooperation between humans and machines."Miodrag Veselic, Technology Manager - openSAFETY, B&R