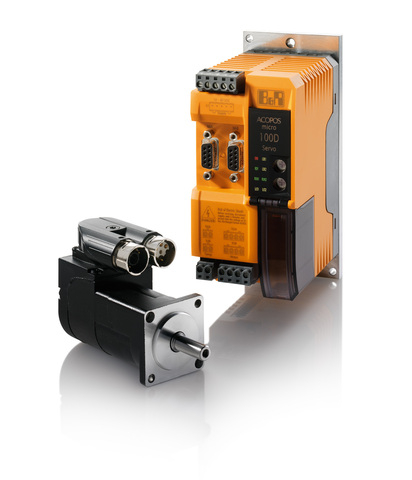
ACOPOSmicro drive system
ACOPOSmicro provides drive modules for up to 2 axes for low-power applications. The ACOPOSmicro is designed to control both stepper motors and servo motors.
- Extremely versatile
- Integrated I/O
- Compact design
- Low power loss
- Uniform design for inverter and stepper motor modules
Stepper motor modules
Inverter modules
パワーサプライモジュール
制動抵抗器
端子台セット
Terminal blocks
Cables
Cable extensions
Batteries
Hose clamps
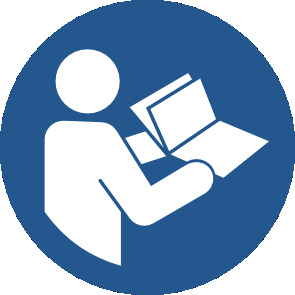
Documentation
Flexibility
Ever-changing fields of application and the necessity to integrate different types of drives in one machine often create enormous challenges for application developers. Creating projects with B&R Automation Studio makes it possible to handle a wide range of drive concepts using the same tools. This means that flexible drive architectures can be implemented by either combining these concepts together or maintaining their independence from one another.
It is possible to plan for different machine variants as early as the project development phase and to account for separate configurations that use various drive types. This makes it easy to switch from a stepper motor to a power inverter variant (and vice versa) without problems. As a result, machine manufacturers are able to enjoy unprecedented flexibility.
Integrated I/O
In addition to trigger inputs, this system also includes a 24 VDC output. It can be used, for example, to control external brakes in addition to being available for other tasks. If required, additional functionality can be added via optional modules without taking up extra space.
This makes it possible to meet even extraordinary customer-specific requirements. The optional support of many different encoder systems illustrates this product line's high degree of flexibility.
Smallest dimensions
The two-channel variant of this system clearly highlights this module's extremely compact design. The ACOPOSmicro requires an area of less than 50 cm² per axis.
This not only saves space in the control cabinet for applications with multiple axes, but also provides advantages in wiring since the bus and supply voltage connection is only required for every second motor.
Such high power density in such a small space is extremely rare.
Variable rated voltage ranges
To achieve higher torque values at high speeds, the first voltage variant was designed for a nominal voltage of 80 VDC. The ability to withstand overvoltage up to 95 VDC also allows for increases in the DC bus voltage such as those that occur during braking procedures. But the drive can also be used for almost any application in the extra-low voltage range. This means that the ACOPOSmicro product family can be operated up to a voltage of 18 VDC.
For servo and stepper motors
Modules from the ACOPOSmicro product family are used to control up to two motors. Stepper motors from a wide range of 24 to 64 VDC ±25% nominal voltage and up to 10 A (15 A peak) motor current can be connected. For servo motors, continuous current of 8 A and peak current of 15 A are permitted.
The modules are protected against overcurrent, overtemperature and other prohibited operating conditions. Appropriate warnings and error messages are output via the fieldbus.