A mature market and tightening regulatory constraints have increased demands on seed processing quality. Recognizing that these demands could no longer be met with the digitally isolated machinery typical of the industry, Dynavia developed a smart seed processing line equipped with a full B&R solution and APROL factory automation.
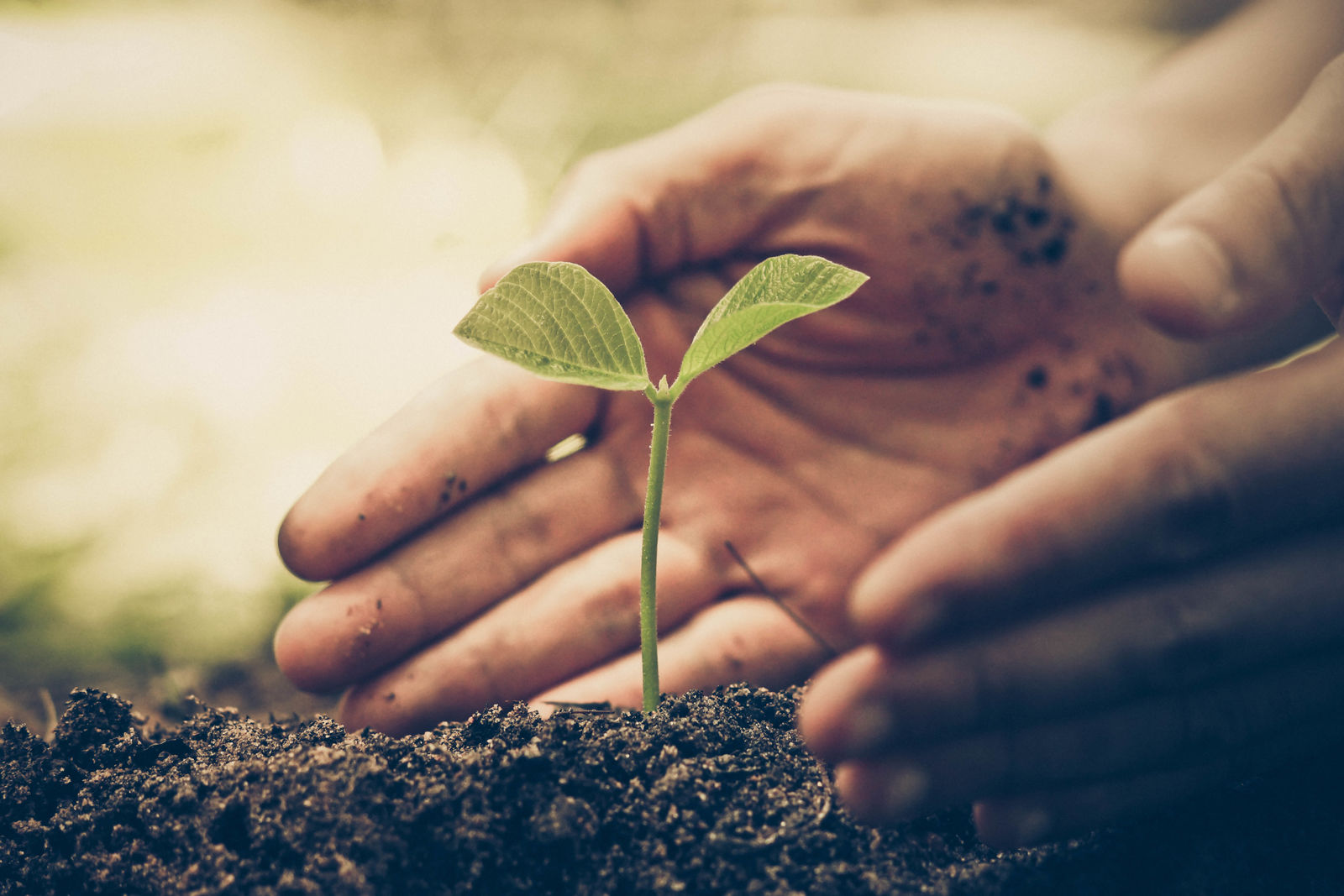
Seeds require a lot of care. Once they have been harvested and checked against specifications for varietal purity, sanitary quality and germination potential, they need to be dried, sorted, cleaned, treated with phytosanitary products and packaged. The various machines required to complete these steps have traditionally been grouped into complex, heterogeneous processing lines with little connectivity between them.
As a result of the complex, rigid architectures of these conventional lines, seed quality has relied heavily on the skill of experienced operators to perform the necessary checks and adjustments. To reduce this risk, seed processing plant builder Dynavia implemented a smart new line concept featuring a complete B&R solution and the APROL factory automation system.
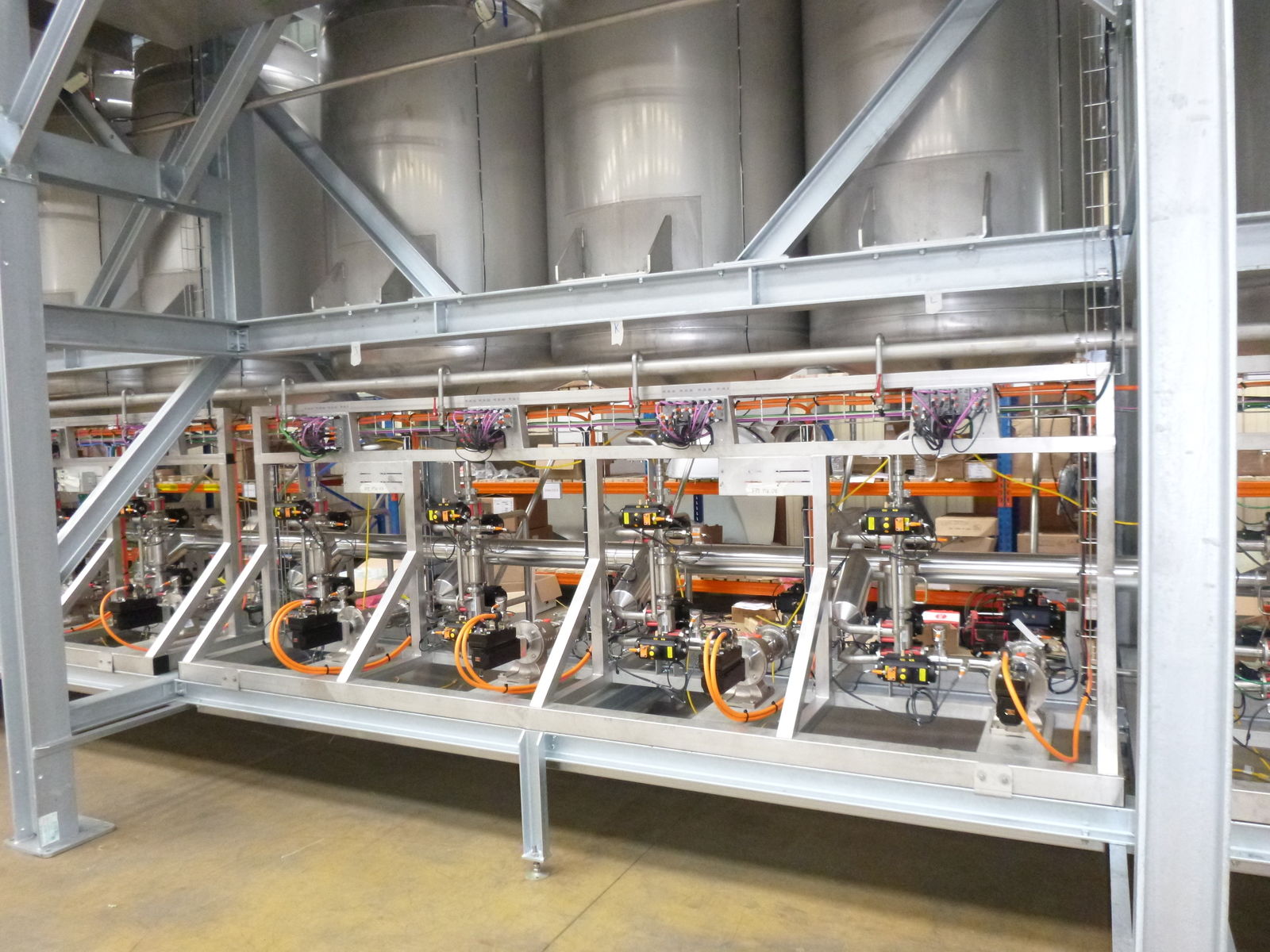
A totally new approach
Recognizing that conventional seed processing lines were approaching their limits, Dynavia developed a groundbreaking new solution with seamless communication between the equipment, controllers and sensors. The new line, unprecedented in the seed processing industry, has already brought substantial gains in productivity and flexibility for end users.
The new line also features a fully automatic cleaning system that enables machines to clean themselves with no operator intervention. When the machine detects a soiled flowmeter, for example, it will allow the current batch to complete and then switch to self-cleaning mode. This self-contained, automatic cleaning process reduces pollution both on the fields and at industrial sites while also decreasing sanitary risks.
All the info at a glance with APROL
"The APROL factory control system and the completeness of the B&R portfolio were decisive factors for us to rely on this company as our automation supplier and partner," says Dynavia President Steven Le Garrec. "Having all the components from a single source gave us the full benefit of their integrated systems allowed us to implement our concept of smart lines in the most efficient way."
The smart processing line Dynavia recently implemented for a major customer is fitted with three thousand I/O points and numerous controllers from B&R's X20 range, all controlled by two redundant APROL runtime servers running on B&R industrial PCs. This line comprises several units for storage and dosing of the phytosanitary products and recipe handling, as well as various mixers, a packaging machine and a palletizing robot.
"APROL integrates control of all the equipment and displays the data in such a way that we can understand and analyze physical phenomena very quickly," reports Le Garrec. "The APROL TrendViewer has allowed us to record process data during the liquid and gas phases and thereby fine-tune the machines faster than ever." Integrated analysis and reporting based on Jaspersoft provides powerful insight into the line's chemical processes.
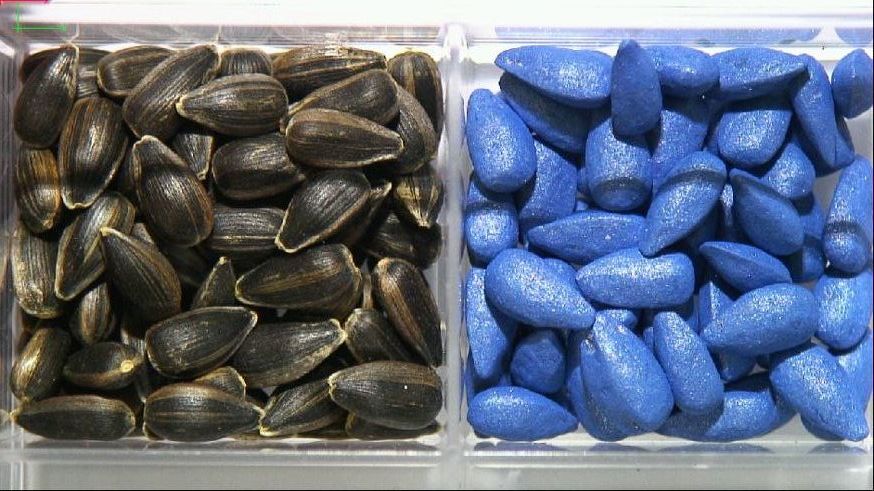
Precision guaranteed by IO-Link and POWERLINK
Because of heightened quality requirements and the tightening regulations on usage and dosage of chemical products, high precision and repeatability have become essential requirements for seed processing lines. In the application described above, regulatory authorities require that chemical products are dosed with a precision as low as one gram per hectare. To achieve this consistently, Dynavia has developed advanced dosage algorithms and taken full advantage of its B&R systems.
"The IO-Link modules in B&R's portfolio allow us to benefit from the added precision of digital sensors," explains Le Garrec. Measurement data delivered by IO-Link sensors only goes through one A/D conversion instead of three with conventional sensors, and the fully digital connection offers extended diagnostic capabilities and easy sensor configuration. "IO-Link connectivity allows us to configure sensors and actuators dynamically, giving us total control over temperatures, levels and pressures at all times, which is essential to meet the new demands on seed quality."
At the control level, the real-time network must guarantee that sensor signals are handled quickly enough to allow the actuators to respond without any loss of precision. In the solution already running at Dynavia's customer, the real-time POWERLINK bus system ensures exceptional output rates and has reduced control loop times to 4 milliseconds. The high performance of this network also allows Dynavia to use brushless motors instead of conventional induction motors, thus ensuring faster actions on the actuator side.
"Our solution achieves a dosage precision of less than one gram, which is very close to the limit of the sensors themselves," reports Le Garrec proudly. B&R's single-cable ACOPOSmotor servo actuators bring Dynavia all the benefits of B&R's decentralized motion technology in terms of reduced cabling and simplified architecture.
Plug-and-play maintenance
"Without a doubt, POWERLINK and IO-Link are a perfect match," confirms Le Garrec, noting that both standards offer plug-and-play features that make maintenance much easier and safer. "It's no longer necessary to travel to the customer's site to switch out a component, which is a major advantage for our export activities. Operators only need to exchange the faulty component and reconfiguration is handled automatically."
Beyond the plug-and-play features, and in line with the concept of smart machinery, Dynavia is developing spare parts utility software based on B&R's fully integrated Automation Studio software environment. This tool runs directly on the machines, and the user interface indicates which parts need to be replaced and allows users to place the necessary order.
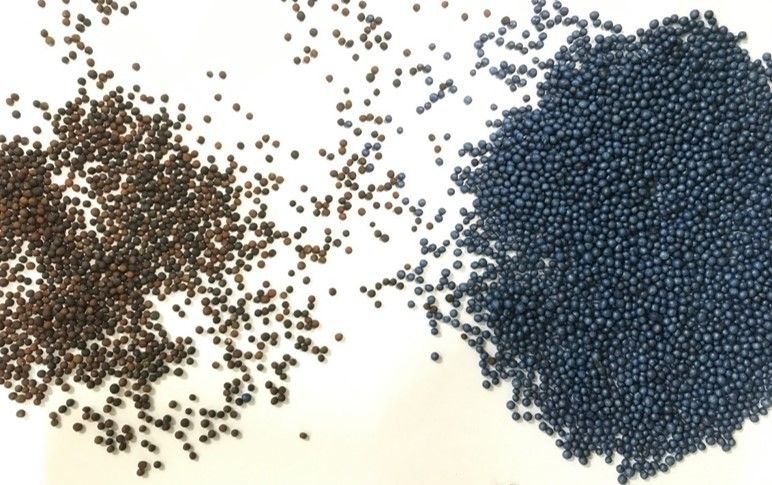
Mass customization with flexible automation
Dynavia's newest installations allow seed producers to implement recipe changes on the fly to handle varying requirements for seed type, quantity, treatment and more. "Our customers are now able to customize their production to an increasing variety of requirements in a highly productive and profitable way," says Le Garrec.
"With the complex, heterogeneous architectures they used in the past, our customers would avoid making any changes to the automation system once it had been set up. The risk of destabilizing the process was just too high," says Le Garrec. "With B&R's integrated solutions, they can now safely and easily adapt the automation solution to their needs."
Cloud-based analytics for predictive maintenance
Dynavia is also working on a predictive maintenance solution to be completed in the near future. On their installations, APROL continuously records around 11,000 pieces of data. To make efficient use of this big data volume, Le Garrec is looking to implement a private cloud solution offered with APROL.
"At the installation level, our big data solution will consist of local APROL systems recording the event history and pushing data – 100 megabytes a week in our case – to a private cloud. An APROL instance located at our premises will store and manage this data. Thanks to the OPC UA and MQTT standards used, all data exchanged with the private cloud is secure."
Advantages of POWERLINK
The combination of the real-time POWERLINK bus system and IO-Link has allowed us to break new records of speed and precision. The high performance of this network also allows Dynavia to use brushless motors instead of conventional induction motors, thus ensuring faster actions on the actuator side.
Steven Le Garrec President, Dynavia "The APROL factory control system and the completeness of the B&R portfolio were decisive factors for us to rely on B&R as our single-source automation supplier. The combination of POWERLINK and IO-Link has allowed us to break new records of speed and precision. The unmatched competence and responsiveness of the local B&R team helped us complete our complex project amazingly fast." |
Automation Studio als Dienstprogramm für Ersatzteile Mit der Software Automation Studio von B&R entwickelte Dynavia ein Dienstprogramm für Ersatzteile. Damit kann festgestellt werden, welche Teile getauscht werden müssen. Die Anwender können die erforderliche Ersatzteilbestellung sofort in Auftrag geben - das spart Zeit und Geld. |