A feed module for an assembly line is typically designed to produce a specific product. Any changes to the product during the design and commissioning phase send developers back to the drawing board and add substantial delays to machine delivery. With an openROBOTICS solution from B&R and COMAU, the versatile new FlexiFeed from Elettrosystem brings long-awaited benefits to OEMs, system integrators and end users alike.
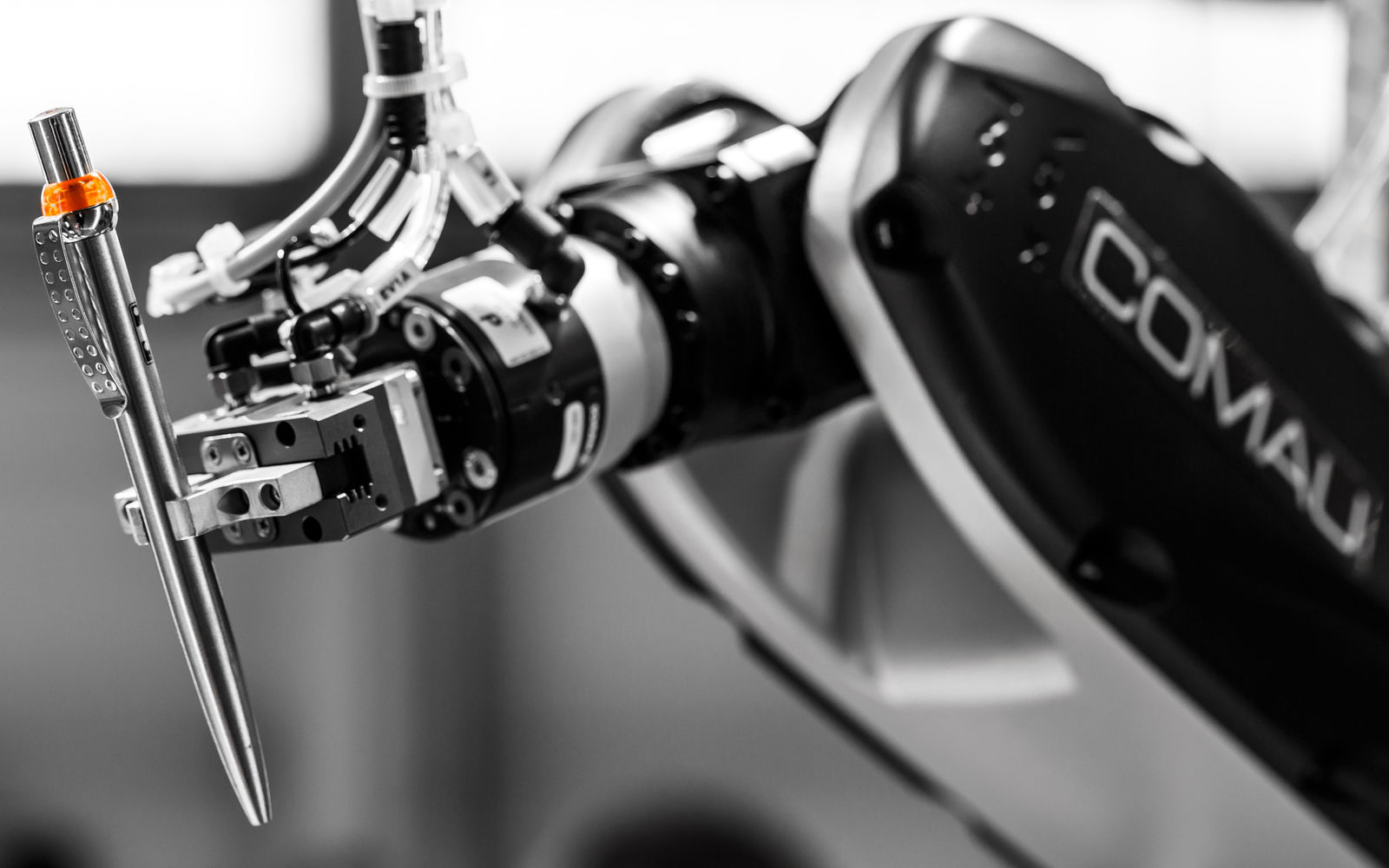
To build a feeder module for an assembly line, you normally need to have a clear definition of all the parts of the machine and a fixed product to be assembled. Commissioning of the machine alone can take from 8 to 12 weeks, and in the event of changes to the product during the development phase, you would need to redesign the machine to adapt it to the new application, adding time and cost to the project.
With the innovative FlexiFeed concept developed by Elettrosystem, this inflexibility is now a thing of the past. As its name suggests, FlexiFeed is able to supply an assembly line with items that vary in shape and geometry. The same machine can be set up for a variety of different products without having to be designed specifically for each one.
Benefits for integrators, OEMs and end users
Founded in 1980 in the hills of Italy's Piedmont region, Elettrosystem specializes in turnkey assembly line solutions. With its range of patented materials and assembly processes, the company has earned a reputation as a global industrial engineering partner for automation. In addition to its primary market in the automotive industry, Elettrosystem's extensive experience in assembly, vision inspection, handling and functional testing is also highly valued in the electromechanical, measurement and instrumentation, general purpose and biomedical fields.
With the company's innovative new feeder, system integrators can start developing the machine before the product is even available in its final release. This reduces the overall machine delivery time and helps achieve lean manufacturing objectives. OEMs are now able to use the same machine for different products by simply changing out the gripper fingers. For end users, eliminating unnecessary downtime brings a significant increase in production capability
For the new feeder to be successful, Elettrosystem needed a robotics and automation solution that was up to the challenge. Many international brands were evaluated in search of a partner with not only the best products, but with a high level of technical expertise and experienced engineers in the field.
One feeder, many products – openROBOTICS
Elettrosystem found what it was looking for with the openROBOTICS solution from partners B&R and COMAU, which combines B&R's full array of intelligent automation components – from PLC, I/O and HMI to machine vision and open communication – with COMAU's high-precision robotics.
"B&R and COMAU have become more than just suppliers – they are two reliable partners who have joined us on a continuous path of shared growth," says Daniele Buttaci, ICT manager & controller at Elettrosystem. openROBOTICS offers a completely uniform solution with highly integrated programming for every component in the line, including the robotics. Thanks to B&R's Automation Studio software development environment and the mapp Technology package, customers simply select the desired COMAU robot in the project environment and it is effortlessly incorporated in – and perfectly synchronized with – the machine's automation software.
Unlike the traditional solution, where robotics and machine control rely on separate controllers or gateways, the open technology from COMAU and B&R allows customers to benefit from a coordinated, holistic approach to operation, diagnostics and maintenance.
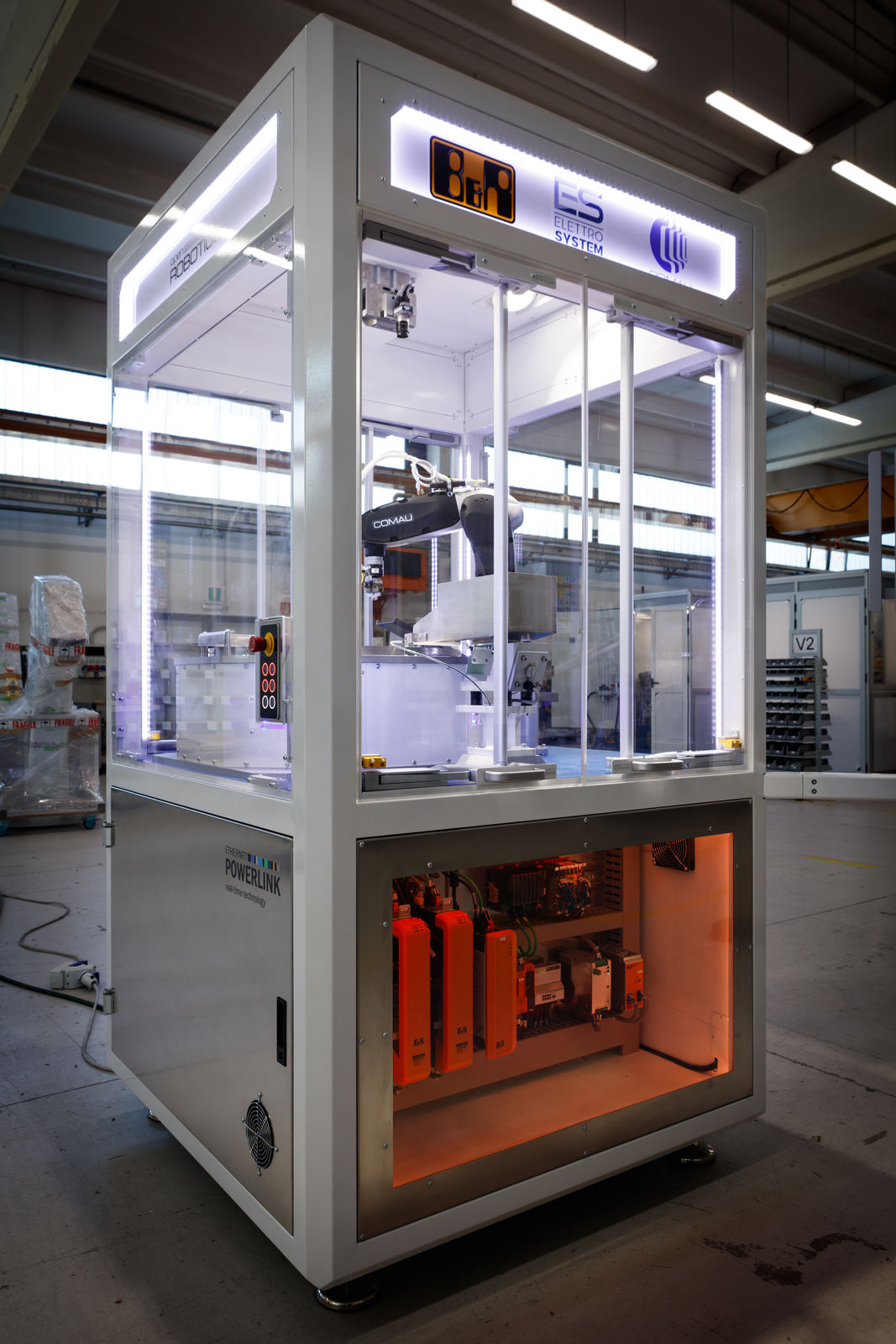
Perfect integration in assembly lines
FlexiFeed is available in three variants: FF3, FF6 and FF9, for processing items with maximum dimensions of 30, 60 and 100 millimeters, respectively. Processing begins when the operator fills bulk items into the hopper, which releases them gradually onto the turntable to prevent jams. The turntable separates and transports the items to the picking area. Here, a camera determines the position and orientation of each item so that a COMAU robot (anthropomorphic, SCARA, delta or Cartesian) can manipulate them correctly for subsequent processing.
Conventional solutions typically require dedicated controllers for CNC and robotics, whereas B&R's integrated solution features a single X20 controller for all of the FlexiFeed's automation – including not only PLC, HMI, communication and vision, but CNC and robotics as well. "This is one of the main highlights of the FlexiFeed," notes Buttaci. "To set up the process, you have only one operator HMI for the robot, camera and turntable." One B&R X20 controller can manage up to three FlexiFeed modules at a time.
B&R's Automation Studio software development environment allows programming in all IEC 611-3 languages, as well as C++, G-code and robotic languages. "We're able to program the robots in G-code with perfectly smoothed movements – which is normal for a robotics environment, but not common in CNC controllers," explains Buttaci. "With so much freedom in the choice of programming languages, we're able to come up with the exact right solution for any task."
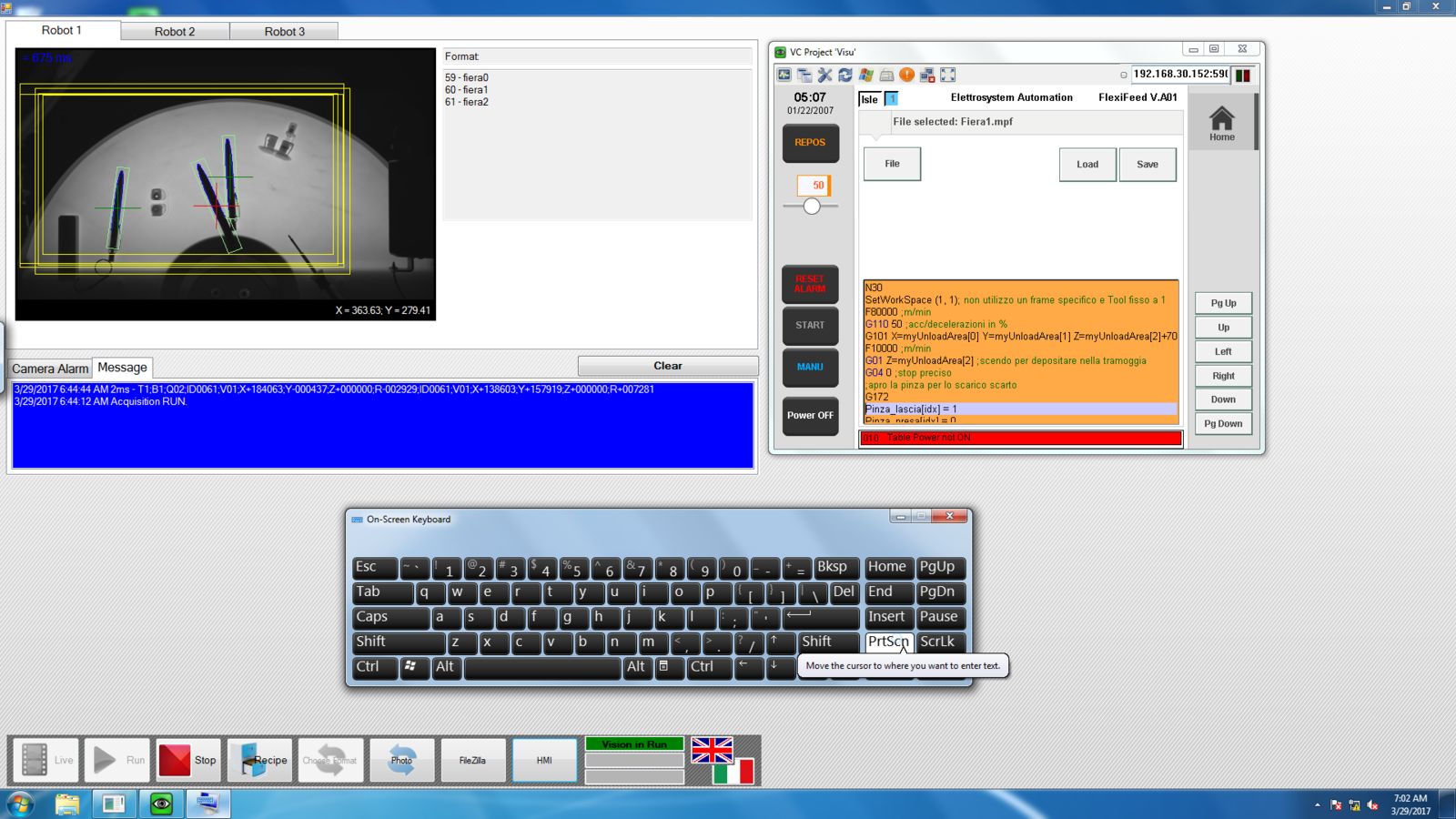
Smaller footprint with maximum power density
With industries demanding ever more compact manufacturing equipment, reducing the number, size and complexity of automation components becomes an important design challenge. The COMAU control cabinet solves this challenge with advanced B&R products like the ACOPOS P3.
Since each ACOPOS P3 device can control up to three axes, COMAU needs only two drives to handle a 6-axis robot. Thanks to the short cycle time of 50 microseconds for current, speed and position control, in combination with the high bandwidth and determinism of POWERLINK, the ACOPOS P3 offers highly dynamic and precise performance for robotic applications.
Flexible assembly done right
With its openROBOTICS solution, the FlexiFeed offers end users numerous advantages – from its compact footprint and easy integration into existing lines to its significantly reduced downtime, easy diagnostics and unmatched flexibility. "Traditional bulk feeding systems, particularly for light plastic parts, have an intrinsically low production efficiency of around 75 to 85 percent," says Buttaci, "so by boosting efficiency to as high as 97 percent, the FlexiFeed offers an immense advantage in terms of production capacity."
OEMs benefit from reduced design and commissioning times thanks to COMAU's wide range of fully interoperable openROBOTICS mechanics and B&R's versatile portfolio for perfect control of any COMAU robot, fully integrated in the same environment and controller as all other automation components. "What's also important to us," adds Buttaci, "is that – although the system is open for integrators and end users to configure it for their particular production process – all of Elettrosystem's technological know-how is securely protected."
One network for all systems
POWERLINK provides a single, consistent and integrated solution for handling all of the FlexiFeed's communication tasks with a single network – from PLC, I/O and sensors to the machine vision system and of course the COMAU control cabinet.
![]() | Daniele Buttaci ICT Manager & Controller, Elettrosystem "B&R and COMAU have become more than just suppliers – they are two reliable partners who have joined us on a continuous path of shared growth." |